ppPLUS: Technologies and more
Go to Homepage to browse companies and process data
ppPLUS-Solutions providing Services and Support
Register creating your own models
Technology
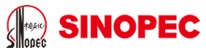
- Name
- Sinopec S-MTO
- Owner
-
/ Sinopec Engineering (Group) Co., Ltd. - Brand
- S-MTO
- Process
- Olefin processes
- Type
- Methanol To Olefins
- Available
-
Process Description
The S-MTO Process includes a Methanol Conversion part and a Light Olefins Recovery part. The Methanol Conversion part includes:
- Raw Material Preheating Unit
- Reaction-Eegeneration unit,
- Quenching Unit
- Thermal Unit.
The Light Olefins Recovery part includes:
- Product Gas Compressor Unit
- Cold Separation Unit
- Thermal Separation Unit
- Propylene Refrigeration Compressor Unit
- Torch system
The heated Methanol Feedstock converts into Products over a specially designed SMTO Catalyst in a Fluidized Bed Reactor. Reactor Effluent is then washed and cooled to remove Catalyst Fines and recover the heat in the Quenching Unit. The deactivated Catalyst is regenerated in a Regenerator and recycled for Re-use. After Compression, the Product Gas enters the Washing Column to remove Oxygenates and Acidic Constituent. After Drying, the Product Gas enters a De-ethanizer, the Gas Phase from De-ethanizer Overhead is sent to the De-methanizer, the Liquid Phase from the De-ethanizer Bottom is sent to the De-Propanizer. The Gas from the De-methanizer Overhead enters the Fuel System. The Stream from the De-methanizer Bottom enters the C2-Splitter to separate Ethylene and Ethane. The Gas Phase from the De-propanizer Overhead enters the C3-Splitter to separate Propylene and Propane. The Stream from the De-propanizer Bottom enters the De-butanizer to separate C4s and C5+ Fractions.
The main parameters of S-MTO Process Technology are shown in Table 1.
Table 1 - Main Process Parameters of S-MTO Process Technology
Reaction temperature, ºC 450-500 Reaction pressure, MPa (G) 0.08-0.25 Regeneration temperature, ºC 600-700 Regeneration pressure, MPa (G) 0.08-0.25 WHSV, h-1 7-12 Features of Technology
With a high performance SMTO Catalyst and a Fluidized-Bed Reactor, the Loss of Catalyst is less than 0.25 kg/t Methanol. The Methanol Conversion is more than 99.98 wt%. The selectivity of Ethylene and Propylene can reach 81 wt%, and the Consumption of Methanol is about 2.98 t/t (Ethylene+Propylene).
The ratio of Ethylene to Propylene can be adjusted from 0.9 to 1.1 (wt/wt) with high yield and high productivity output.
Crude Methanol is also applicable, which can reduce the cost of Methanol Purification Unit.
Front De-ethanization Process is adopted in S-MTO Process for Olefins Recovery. The purity of the Ethylene and Propylene Products can meet the requirement of Polymerization Grade Monomer with a recovery rates higher than 99.8 % respectively.
Catalyst
S-MTO Technology adopts SINOPEC proprietary SMTO Catalyst which is based on a Silicoaluminophosphate Zeolite as its active Component. The SMTO Catalyst has the advantage of high selectivity, high diffusion rates, large surface area, good stability and attrition resistance. The SMTO Catalyst has been applied in a Methanol To Olefins Plant with capacity of 600,000 tons/year in Zhongyuan Petrochemical Company, Henan province, China. Stable long-cycle Run length has shown that selectivity of Ethylene and Propylene is about 81 wt% and Methanol Conversion is more than 99.98 wt%.
Investment Estimate
At Chinese price level of 2015, the investment of building a 1,800,000 tons/year S-MTO Plant in China is about RMB 2.6 billion.
Source: VCDC, Advanced Value Chain Development Center, Dec 2018 Upload, S-MTO Methanol to Olefins Technology, SINOPEC
- Link
System Info
- Updated by
-
 Kokel, Nicolas
- Updated
- 3/4/2023 4:34 PM
- Added by
-
 Kokel, Nicolas
- Added
- 3/4/2023 2:39 PM

No Services yet available.
Enquire in Solutions how we can help you.
Technology Unit |
---|
C2-Splitter |
C3-Splitter |
Caustic Wash |
De-C1 |
De-C2 |
De-C3 |
De-C4 |
Quench Tower |
Reactor |
Regenerator |
Water Wash |