ppPLUS: Technologies and more
Go to Homepage to browse companies and process data
ppPLUS-Solutions providing Services and Support
Register creating your own models
Technology
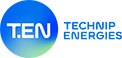
- Name
- Technip Steam Cracking
- Owner
-
/ Technip Energies NV - Brand
- Technip SC
- Process
- Cracking
- Type
- Steam Cracking
- Available
-
Ethylene Plants
Technip Energies designs and builds ethylene plants and does as well plant expansions, indicating to have built 150 grassroots plants and claiming to own about 50% of the global licensing market[1]. This follows on the acquisition of Shaw’s Stone & Webster process technologies back in 2012[2].
Figure 1 - Sadara Mixed Feed Cracker Design[3]
Cracking Aspects and Parameter Ranges
The company reports the following aspects of Steam Cracking[4]:
- Cracking reaction is non catalytic and not selective.
- Cracking reaction is highly endothermic.
- Inlet temperature: 550-700°C.
- Outlet temperature: 750-900°C.
- Selectivity sensitive for residence time, lower is better.
- Selectivity sensitive for pressure, lower is better.
- Furnace outlet pressure at TLE: 0,5 – 1,5 barg.
- Dilution steam is required; ratio between 0,25 – 1,0.
- Radiant coil material: 25/35 and 35/45.
In particular, products yields depending on feedstock are reported as shown in Table 1. These are product yields in the cracked gases at the exit of the furnace, not accounting for alcanes recycle[4].
Table 1 - Products yields from ethane and naphtha cracking
Mass, dry% Ethane Naphtha Hydrogen 4.1 0.8 Methane 5.0 13.4 Acetylene 0.4 0.3 Ethylene 52.8 27.7 Ethane 32.6 3.8 C3H4's 0.03 0.6 Propylene 1.2 16.4 Propane 0.2 0.5 Sum of C4's 1.9 11.2 Sum of C5's 0.4 5.9 Sum of C6's 0.9 8.1 Sum of C7's 0.1 4.1 Sum of C8's 0.1 2.2 Sum of C9's 0.01 1.4 Sum of C10's 0.2 3.4 TOTAL 99.94 99.8 Proprietary furnace technologies
The following furnace technologies are proprietary, with design capabilities of over 300,000 tonnes[1]:
- Gas cracking
SMK™ and Ultra Selective Conversion (USC®) M-coils are the preferred option for high-capacity, low-cost, and reliable operations. These technologies have been installed in more than 180 furnaces. - Liquid cracking
GK6® and USC® U-coils are designed for short-residence time. These technologies, which can be used in new furnaces or to modernize existing furnaces, have been applied in over 100 furnaces over the past 10 years. - SFT® (Swirl Flow Tube) Technology
This technology, which uses helical tubes that enables improved thermal exchange coefficients, can be used in all furnaces to further improve performance (selectivity, capacity and run-length). - Triple-Lane Radiant Coil Designs
This patented technology has been developed by Technip Energies. Radiant coils are arranged in three lanes, with one outlet lane and two inlet lanes. This design is applicable to both gas and liquid furnaces, and allows for greater capacity and/or run-length in a given firebox size.
Cracking furnace layout and design
The cracking parameters are presented in Fig. 2 and the furnace layout is shown in Fig. 3[4].
Figure 2 - Cracking parameters
Figure 3 - Cracking furnace layout
Proprietary equipment
The following pieces of equipment are proprietary[1]:
- TRANSFER LINE EXCHANGER (TLE)
This exchanger safely recovers heat from furnace outlets without fouling to produce very high-pressure steam. - BURNERS
Burner designs for low NOx emission, developed in-house (Large Scale Vortex (LSV®) burners for bottom burners, Side wall burners). - RIPPLE TRAY™ TECHNOLOGYHIGH PERFORMANCE EXCHANGERS
High-capacity trays used in fouling services and/or to increase production capacity. Over the past 50 years, the technology has been used in almost 500 applications worldwide. - QUENCH FITTING
Provides high efficiency, direct-contact quenching of furnace effluent gas with a process hydrocarbon liquid stream to obtain the desired mix, rapidly and completely. - VAPOR FLUTE™
Proprietary device, component of many quench oil and/or quench water tower grassroots and revamp projects, that increases operational efficiency by improving distribution and acting as a first line of defense against liquids and coke that enter the tower. - ANTI-COKING HEAVY FEED MIXER™
The mixer vaporizes heavy hydrocarbon feedstocks. It uses a unique patented anti-coking design that minimizes the coking tendency and required length of the mixing chamber. - HIGH PERFORMANCE EXCHANGER
Through an agreement with Wieland to jointly market innovative enhanced heat exchangers for ethylene plants for further reduction in energy consumption and CO2 emissions. These exchangers can be used either for boiling or condensing applications.
Separation technologies
The Separation Technologies offered comprise[1]:
- Quench oil tower equipped with reliable/fouling resistant Ripple Tray™ technology.
- Packed quench water tower to minimize ΔP.
- Four or five stage cracked gas compressor at low suction pressure to optimise furnace yields.
- Caustic tower with Ripple Tray™ technology for fouling minimisation.
- Dual depropanisers for efficient/reliable fractionation.
- Cold section with proprietary Heat Recovery System (HRS) and dual demethaniser columns for high energy efficiency.
- Heat pumped low pressure two feed C2 splitter integrated with ethylene refrigerant.
- Heat pumped or conventionally reboiled C3 splitter.
- Cascade single component refrigeration (ethylene and propylene or propane) – easier start-up than combined refrigeration systems and preferred for energy optimization.
Acetylene conversion technologies
Two proven acetylene conversion technologies are available to obtain up to 2 million tonnes of ethylene[1]:
- Front-end hydrogenation, coupled with either a front-end de-ethanizer or a front-end de-propanizer, is available for gas or liquids crackers.
(references: Sadara, PetroRabigh in the Kingdom of Saudi Arabia). - Back-end hydrogenation, coupled with a front-end de-methanizer, can be used in either gas or liquids crackers. This technology is currently in use in many operating plants, including the Yansab plant in the Kingdom of Saudi Arabia.
References
- Technip Energies 2024, Ethylene brochure.
- NS Energy Staff Writer, 2nd Sep 2012, Technip acquires Shaw’s Stone & Webster process technologies.
- TechnipFMC 2017, Ethylene Production brochure.
- Jelle Gerard Wijnja, 31st OCt 2017, New Technologies in Ethylene Cracking Furnace Design, TechnipFMC, AIChE NL/B
- Link
System Info
- Updated by
-
 Braun, Uwe
- Updated
- 4/26/2024 11:30 AM
- Added by
-
 Kokel, Nicolas
- Added
- 3/2/2022 6:00 PM

No Services yet available.
Enquire in Solutions how we can help you.
Entity | Site (Country) | Asset (Plant) | |||
---|---|---|---|---|---|
![]() |
![]() |
|
MFC | ||
![]() |
![]() |
|
Ethane Cracker | ||
![]() |
![]() |
|
ECR | ||
![]() |
![]() |
|
Ethane Cracker | ||
![]() |
![]() |
|
ROG Cracker | ||
![]() |
![]() |
|
Gas Cracker | ||
![]() |
![]() |
|
Ethane Cracker | ||
![]() |
![]() |
|
Mix Feed Cracker | ||
![]() |
![]() |
|
N°1 Cracker | ||
![]() |
![]() |
|
N°2 Cracker | ||
![]() |
![]() |
|
N°3 Cracker |