ppPLUS: Technologies and more
Go to Homepage to browse companies and process data
ppPLUS-Solutions providing Services and Support
Register creating your own models
Technology
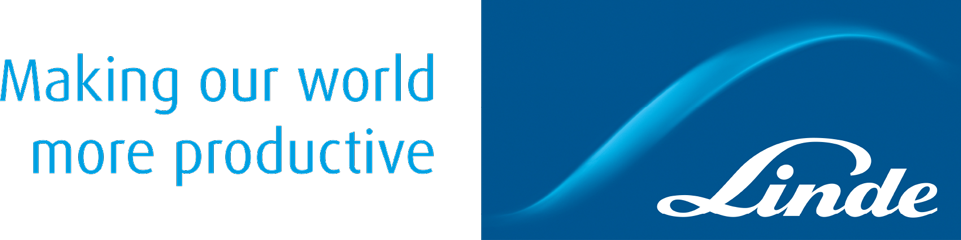
- Name
- Linde Steam Cracking
- Owner
-
/ Linde plc - Brand
- Linde Steam Cracking Technology
- Process
- Cracking
- Type
- Steam Cracking
- Available
-
Steam Cracking Technology
They involve cracking hydrocarbon feedstocks in the presence of steam and at temperatures of between 800° and 870°C. The resulting cracked gas is separated into valuable products such as ethylene, propylene, acetylene, butadiene, pyrolysis gasoline and BTX, all according to the specifications required for downstream processes[1].
Linde Engineering has licensed and built a series of ethylene plants with capacities of 1,500,000 tonnes per year, and has expanded its references to include plants that produce as much as 2,300,000 tonnes per year of ethylene. To date, Linde has licensed and/or built more than 70 plants around the world[1].
Cracking Furnace Technology
Linde’s proprietary PyroCrack® technology handles the full spectrum of feedstocks - from light hydrocarbons to naphtha and heavy liquids such as gas oils and hydrocracker residues. Feedstock flexibility is easy with the twin cell design, which allows independent cracking of different feedstocks in one furnace. Twin cells can also be designed for decoking – one cell can run in cracking mode while the other operates in decoking mode. Exclusive short-residence time coil designs achieve maximum olefin yields and excellent furnace run lengths.[2].
Figure 1 - Linde Cracking Furnace[2]
In recent years, Linde designed cracking furnace with ethylene production capacities in excess of 250,000 tonnes per year. Linde's proprietary technologies utilize the latest coil geometries and metals, proprietary air preheating concepts, ultra-low-NOx burners and catalytic DeNOx systems to keep emission levels below national and international regulations, maximize yields and minimize energy consumption[1].
Ethylene Separation Technology
Figure 2 - Linde Steam Cracking Process Flow Diagram[3]
Downstream of a cracking furnace, the separation train of a cracker starts with the “hot” section, where the cracked gas is quenched and cooled down to ambient conditions, heavy fractions are condensed and separated, and the process steam is condensed and removed for reuse. The cracked gas then enters the compression section, where it is typically compressed in four to five stages up to a pressure of approximately 36 bar. The compressed, cracked gas is dried and cooled before being separated into the C2 fraction, which is routed to the cold section for further separation, and into the C3+ fraction. C2- and C3+ fractions are then separated in sequential steps into the specified products. Unwanted impurities like acetylene and methylacetylene/propadiene are hydrogenated to ethylene and propylene. Pyrolysis gasoline must also be hydrogenated in order to meet market specifications. In some cases, certain fractions (e.g. ethane, propane and butane/butenes) are recycled back to the furnaces in order to improve the overall product yields[1].
References
- Linde Engineering, Steam Cracking Technology (accessed 27th Apr 2024).
- Linde Engineering, Steam Cracking Frunaces (accessed 27th Apr 2024).
- Christian Ziegle, Plant Operation, Olefin Academy 2010, Munich, Linde.
- Link
System Info
- Updated by
-
 Kokel, Nicolas
- Updated
- 4/28/2024 8:49 AM
- Added by
-
 Kokel, Nicolas
- Added
- 4/27/2024 12:52 PM

No Services yet available.
Enquire in Solutions how we can help you.
Entity | Site (Country) | Asset (Plant) | |||
---|---|---|---|---|---|
![]() |
![]() |
|
Ethylene Plant | ||
![]() |
![]() |
|
Ethylene Plant | ||
![]() |
![]() |
|
Ethylene Plant | ||
![]() |
![]() |
|
Olefin Plant | ||
![]() |
![]() |
|
Naphtha Cracker | ||
![]() |
![]() |
|
Gas Cracker | ||
![]() |
![]() |
|
Olefin 1 | ||
![]() |
![]() |
|
Olefin 2 | ||
![]() |
![]() |
|
DFCU | ||
![]() |
![]() |
|
Ethylene Plant | ||
![]() |
![]() |
|
EPB Cracker |