ppPLUS: Technologies and more
Go to Homepage to browse companies and process data
ppPLUS-Solutions providing Services and Support
Register creating your own models
Technology
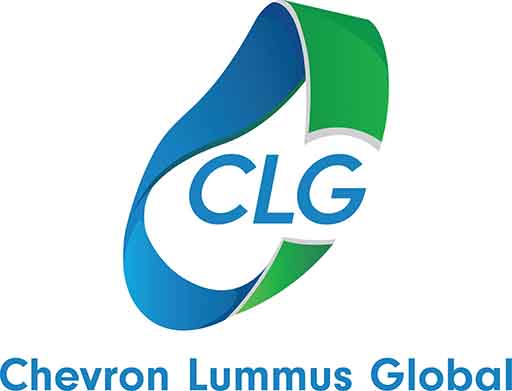
- Name
- CLG ISOCRACKING
- Owner
-
/ Chevron Lummus Global - Brand
- ISOCRACKING
- Process
- Cracking
- Type
- Resid Hydrocracking
- Available
-
CLG's ISOCRACKING Fixed Bed Hydrocracking Technology converts Naphthas, AGO, VGO, DAO, Cracked Oils from FCC Units, Delayed Cokers and Visbreakers, and intermediate Products from Residue Hydroprocessing Units into lighter, high-quality, highly isomerized Products such as LPG, Gasoline, Catalytic Reformer Feed, Jet Fuel/Kerosene, Diesel and Feeds for FCC, Ethylene Cracker or Lube Oil Units (Table 1).[1]
Table 1 - ISOCRACKING produces a highly isomerized Product slate[2]
Heavy Naphtha high ring content >60 LV % Diesel Low pour point
High cetane-30°F (-35°C)
50-62Jet/Kerosene Low freeze point
High smoke point-60°F (-51°C)
25 mm+Waxy Base Oil High VI >110 Ethylene Cracker Feed Low BMCI 6-16 FCC Need Low Sulfur
Low Nitrogen5-300
1-50A broad range of both Amorphous/Zeolite and Zeolitic Catalysts, including Noble-Metal Zeolitic Catalysts, are used to tailor the ISOCRACKING Process to the Refiner’s objectives. In general, the Process involves a Staged Reactor System with an initial Stage of Hydrotreating and partially Hydrocracking the Feed, and a subsequent Stage continuing the Conversion or Product Upgrade Process in a more favorable environment.[1]
Figure 1 - Feed Conversion vs. Catalyst Character[2]
ISOCRACKER is offered in several Designs for all types of Configurations, including:
- Single-Stage Once-Through (SSOT)
- Single-Stage Recycle (SSREC)
- Two-Stage Recycle (TSREC)
ISOCRACKING SSOT Configuration produces Feedstocks with superior characteristics for FCC Feeds, high VI Lubes or Ethylene Plant Feeds. Latest development for SSOT employs a moderately high-pressure Design in conjunction with a tailored Catalyst System that provides Hydrodenitrification and high Hydrocracking activity.
The SSREC configuration is used for high Conversion Processing of light feeds and for low capacity Units, processing Heavy Feeds at low Feed rates.
ISOCRACKING TSREC is optimized for maximum yields of premium Products with minimum Hydrogen Consumption. The First Stage removes feed impurities and converts 20-50% of the Feed. The Second Stage cracks the cleaned Feed at lower temperatures[2].
Figure 2 - ISOCRACKING Two-Stage Recycle Configuration[1]
Most modern large-capacity Flow Schemes involving Heavy Sour Gas Oils require two Reactors (1) & (4) and one High-Pressure Separation System (2) with an optional Recycle Gas Scrubber (5) and one Recycle-Gas ½Compressor (8). The Low-Pressure Separators (3), Product Stripper (6) and Fractionator (7) provide the
flexibility to fractionate products either in between reaction stages or at the tail-end, depending on desired
Product slate and selectivity requirements.[1]1. Jack, 17 Jun 2019, Hydrocracking Process by Chevron, Oil & Gas Process Engineering
2. Chevron Lummus Global, CLEAN FUELS / ISOCRACKING
- Link
System Info
- Updated by
-
 Kokel, Nicolas
- Updated
- 5/20/2023 11:34 AM
- Added by
-
 Kokel, Nicolas
- Added
- 2/22/2023 3:36 PM

No Services yet available.
Enquire in Solutions how we can help you.