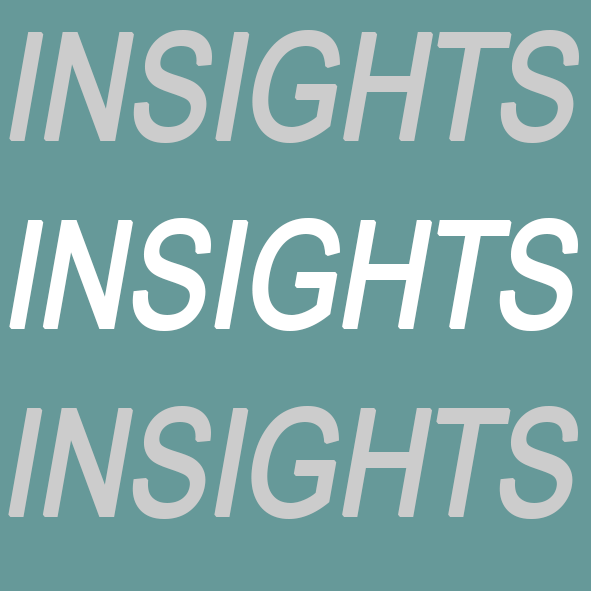
Article
Dealing with LPG Surplus in a Safe and Profitable Way – The New Naphtha Alkylation Technologies
Introduction and Context
The process accident occurred in PES (Philadelphia Energy Solutions) Company in June of 2019 restarts the discussion about the security of naphtha alkylation units based on HF (hydrofluoric acid) as a homogeneous catalyst. In the last years, some refiners have decided to stop the operation of his HF alkylation units due to the unacceptable safety risks.
The high toxicity and corrosion risks associated by hydrofluoric acid require great attention of inspection equipment team to control the integrity of process equipment when this managing system fails the consequence is drastic like it’s possible to conclude based in the previous analysis conducted by CSB (U.S. Chemical Safety and Hazard Investigation Board).
In the last years, some process accidents involving Alkylation units call the attention regarding the safety characteristics of these process units, below we quote the last process safety accidents involving alkylation units:
1 – PES Refinery in USA, 2019
2 - CITGO Corpus Christy Refinery in USA, 2009
3 – Hube Globe Company in South Korea, 2008
4 – Marathon Petroleum Refinery in USA, 1987
5 – Ciniza Oil Refinery in USA, 2004
This short list of process accidents calls the attention of the authorities to the real safety risks associated with the presence of alkylation process units based on HF close to urban centers once a great release of HF can affect the population and cause severe damages and human losses.
It’s interesting to highlight that the naphtha alkylation technology as octane boosting route can be attractive to refiners inserted in markets with high demand of gasoline and availability of LPG like the United States. An interesting case study is the Brazilian market which is historically, Brazil relies on external market to supply their needs of LPG. In 2020 the internal production of LPG in Brazil was 9,86 million m3 where 74 % was supplied by refineries (7,34 million m3) while petrochemical plants and natural gas processing units were responsible for the remain internal production, in the same year, the imports of LPG in Brazil reached 3,62 million m3. With the development of pre salt crude oil reserves the natural gas production in Brazil is growing and the production of LPG associated with the natural gas tends do reduce the external dependence of this derivative. According to Brazilian Petroleum Agency (ANP) the imports of natural gas reduced 20 % in 2020 in comparison with 2019, reaching 7,9 billion m3.
This scenario can lead the Brazilian refiners to consider the naphtha alkylation route as octane boosting to produce low sulfur and high quality gasoline at same time which can deal with a eventual surplus of LPG in the internal market. Considering the growing propylene gap, which is observed at global level, another attractive route to deal with LPG surplus is the propane dehydrogenation (PDH) units that can be applied to add significant value to the LPG.
Gasoline Production Process
The final gasoline is composed by a blending of different naphtha streams, as presented in Figure 1.
Figure 1 – Example of Process Streams Blending to Produce Gasoline
The use of straight run and reformed naphtha is normally minimized, aiming to direct these streams to petrochemical intermediates market due to the higher added value of these streams in this market.
Cracked naphtha (Naphtha from FCC) contributes positively to the octane number of the final gasoline, however, due to the current restrictions related to the sulfur content in the gasoline (maximum of 10 ppm), the use of cracked naphtha without treatment step is limited. Refineries that have catalytic alkylation units in his refining scheme normally direct this stream to produce aviation gasoline that have higher market value when compared with automotive gasoline, for this reason, the participation of the alkylation naphtha is minimized in the composition of this fuel.
Isomerization naphtha has low contaminants content (sulfur and nitrogen) and high octane number and, for these reasons, the participation of this stream in the formulation of gasoline is maximized in refineries that have isomerization units in the refining scheme. In markets with high demand for gasoline, refiners can add butanes to gasoline pool, however, the participation is limited due to the high vapor pressure of this stream that can lead to break quality requirements (Reid Vapor Pressure – RVP). Normally, butanes are added to LPG pool, respecting the limits to avoid breaking the mixture quality related to heavy limitations.
Nowadays, due to the environmental and quality regulations over the gasoline the hydrodesulphurization of cracked naphtha is fundamental to be possible the refiners meet the sulfur content in the final gasoline that can be low than 10 ppm in most restrictive markets. The alkylated naphtha is one of the main octane boosters in the gasoline pool and, according to the refining scheme, is a fundamental stream to refiners achieve the current quality requirements of final gasoline.
Traditional Technologic Routes to Naphtha Alkylation
Gasoline is one of the most consume crude oil derivate and is normally produced through a mixture of naphtha from different refining process steps. The streams normally involved in the gasoline production process are straight run naphtha, cracked naphtha, coke naphtha (after hydrotreatment) and reforming naphtha.
One of the main parameters of gasoline quality is the octane number that is a measure of combustion quality of this derivate, one of the streams that contributes to raising the octane number is the reformed naphtha, produced in the Catalytic Reforming Unit. However, due the severe restrictions related to the carcinogenic aromatic emissions, mainly benzene, some refiners have avoided the application of this stream to formulate gasoline, directing the reformed naphtha preferably to petrochemical intermediates production in aromatics complexes.
An alternative to the reforming naphtha is the production of branched hydrocarbons (with high octane number) through Catalytic Alkylation Process.
The alkylation process involves the reactions between light olefins (C3 – C5) and isoparaffinic hydrocarbons like isobutane. The reaction product called alkylate is a mixture of branched hydrocarbons with higher molecular weight and higher octane number.
An example of typical alkylation reaction is represented below:
C4H10 + C3H6→ C7H16 (2,3 Dimethylpentane)
The reaction is catalyzed in strongly acidic reaction environment, the acids normally employed in the industrial scale technologies are Hydrofluoric Acid (HF) and Sulfuric Acid (H2SO4).
The main advantage of alkylation process is the production of a stream with high octane number, high chemical stability and practically free of contaminants as nitrogen and sulfur. These characteristics turn the alkylate a component attractive to the gasoline formulation to the automotive and aviation industries.
Alkylation process feed streams are generally obtained from LPG produced in deep conversion units, mainly Fluid Catalytic Cracking (FCC) and Delayed Coking. The LPG produced in these process units have high olefins content, ideal for the alkylation process. The isobutane stream is normally obtained through separation of LPG produced in the atmospheric distillation unit, FCC or Delayed Coking in deisobutanizer towers.
As aforementioned, the acids generally employed as the homogeneous catalyst to the alkylation process are HF and H2SO4. Figure 2 presents a process flow diagram to the alkylation process catalyzed by HF.
The feed stream goes through a pretreatment (generally molecular sieves or alumina) before being pumped to the reactor, the objective is to remove process contaminants mainly water, diolefins and sulfur and nitrogen compounds. Water is especially damaging to the process, once accelerates piping and equipment corrosion process, and beyond requires higher HF reposition.
After pretreatment the hydrocarbons streams are put in contact with the hydrofluoric acid in the reactor and the hydrocarbons mixture and HF solution is separated through gravity in a settler vessel, the hydrocarbon phase is sent to the fractionating section while the aqueous phase (containing the most of HF) is cooled and sent back to the reactor. As alkylation reactions are exothermic, the reactor is continuously refrigerated aim to keep the reaction ideal conditions.
Figure 2 – Typical Process Flow Diagram to Catalytic Alkylation Unit using HF as Catalyst
A part of hydrofluoric acid is sent to the stripping column where the acid is stripped with isobutane. The top product is a mixture of HF and isobutene and sent back to the reactor while the bottom stream containing an azeotropic mixture of water and HF, beyond hydrocarbons, this step is responsible to keep the HF free of contaminants and with adequate concentration to the alkylation process.
After the separation columns, butane and propane streams go to a treatment with alumina aim to decompose organic fluorides and with KOH to neutralize the remaining acidity. The alkylate stream is treated with NaOH to neutralize the remaining acidity. Currently, the main alkylation technology licensors with HF are the companies UOP and CONOCO-PHILLIPS.
Alkylate stream is normally directed to the refinery gasoline pool to the production of high octane automobile gasoline or aviation gasoline, however, in petrochemical plants this stream can be used as intermediate to produce ethylbenzene (to produce Styrene), isopropyl-benzene (to produce Phenol and Acetone) and dodecyl-benzene used to produce detergents. Propane and butane streams can be sent to the LPG pool of the refinery or commercialized separately.
The alkylation process with sulfuric acid as catalyst has similarities with the hydrofluoric acid process, however, the sulfuric acid regeneration step is more complex and involves the H2SO4 decomposition in SO2 and SO3 and the subsequent condensation of concentrated sulfuric acid, this regeneration can be conducted in the processing site or in an external process plant, consequently the acid sulfuric consumption in the process is much higher than HF, furthermore, the solubility of sulfuric acid in hydrocarbons is lower, requiring greater agitation to maintain the contact between the phases in ideal conditions to the process.
The alkylation technologies with sulfuric acid most applied in industrial scale are the processes STRATCO Effluent Refrigerated Alkylation Process®, licensed by STRATCO Engineering Company and EXXON MOBIL Cascade Auto refrigerated Process®, licensed by EXXON MOBIL Company. Figure 3 shows a simplified process flow diagram to the alkylation technology with H2SO4, licensed by STRACTO Engineering. Nowadays, the Stratco™ process is licensed by Dupont Company.
Figure 3 – Basic Process Flow Diagram to the Alkylation Process Catalyzed by H2SO4, developed by STRATCO Engineering Company.
Olefins feed stream go to a coalescer to remove water, after the mixture with isobutane recycle, in the sequence the mixture is sent to the reactor. The mixture of hydrocarbons and acid follow to a settler where the phase separations occurs, organic phase is sent back to reactor, a control valve promotes the necessary pressure reduction to vaporize the lighter hydrocarbons and remove heat from the reactor, controlling the equipment temperature which raises due the exothermic characteristics of alkylation reactions.
The hydrocarbons blend is sent to a flash drum where the lighter phase is directed to a compressor to condense in an accumulator vessel and the propane is recovered in the depropanizer tower while the heavier hydrocarbons (essentially isobutane) are recycled to the reactor. The stream containing the alkylate is directed to a caustic treatment and posteriorly to a deisobutanizer column where the alkylate are removed in the bottom.
As aforementioned the need of catalyst replacement is higher in the process with sulfuric acid, however, the HF process needs higher Isobutane/Olefins ratio, which means a greater separation system. Over the last decades, the refiners have opted to the HF alkylation technologies due to the higher simplicity of this process and the lower need of catalyst replacement that leaves to lower operational costs.
However, regulatory pressures have led some refiners to convert her their HF alkylation units to operate with H2SO4, due the high volatility and higher risks presented by the hydrofluoric acid, some licensers developed technologies to convert HF units to operate with sulfuric acid like the ALKYSAFE® technology, licensed by STRATCO Engineering Company and the ReVap® process, developed by the companies EXXON MOBIL and CONOCO-PHILLIPS which uses additives to reduce the HF volatility, making the unit operation safer.
The principal process variables of the alkylation process are the isobutane/olefins ratio, reaction temperature, acid/hydrocarbon ratio, acid purity, residence time in the settler and operation pressure.
To alkylation processes with HF, the reaction temperature varies from 20 to 40 oC while sulfuric acid processes operates under lower temperatures, among 4 and 10oC, under higher temperatures the sulfuric acid can suffer decomposition to SO2 – SO3. Operating pressure is generally sufficient to keep the hydrocarbons in the liquid phase, normally lower than 5 bar. The residence time in the settler is important because if this time is quite low, undesirable reactions can occur as organic fluorides production, in the case of HF which raises the catalyst consumption and reduces the alkylate production.
Acid purity must be maintained higher as possible through the removal of ASO (Acid Soluble Oil), water and dissolved reactants in the HF case and through fresh acid replacement in processes with acid sulfuric as the catalyst.
The main disadvantage of the alkylation processes with homogeneous catalyst (HF or H2SO4) is the need to handling strong acid highly concentrated, that leave a greater process safety risks and high maintenance costs, mainly related to avoid corrosion in piping and equipment and, as aforementioned, equipment failures with contention losses can have dramatic consequences.
Alternatives and Safer Technologies to Naphtha Alkylation
Aiming to eliminate these risks, some licensors have dedicated his efforts to develop heterogeneous catalysts that can replace the strong acids in the alkylate production processes, the UOP Company developed the process called Alkylene™, that apply a solid catalyst with continuous regeneration during the process. Among other technologies can be cited the processes LURGI EUROFUEL™, developed by Lurgi Engineering Company in cooperation with SUD-CHEMIE, the ALKYCLEAN™ process, developed by the companies ABB-Lummus and Akzo Nobel and the process FBA™, developed by Haldor Topsoe. Figure 4 shows a process scheme to the Alkylene™ technology, licensed by UOP Company.
Figure 4 – Process Arrangement for Alkylene™ Technology, developed by UOP Company (Encyclopedia of Hydrocarbons, 2006)
Another attractive technology to alkylation developed by UOP Company is the ISOALKY™ based on the ionic liquid catalyst and it’s possible to revamp the conventional liquid acid units to apply the new technologies. The heterogeneous catalyst applied in substitution of liquid acids are based on zeolites and as presented above can offer higher operational safety to refiners and adjacent communities once eliminate not only the process risk but also all logistic and handling of strong acids like HF and H2SO4. Even refiners with low capacity of capital investment are looking to change the HF by sulfuric acid (H2SO4) as the catalyst in his processes once the sulfuric acid is present lower toxicity than hydrofluoric acid (HF). Another interesting technology dedicated to produce alkylated naphtha through safer route is the Alkysafe™ process also developed by UOP Company which applies ionic liquids as homogenous catalyst against strong acids in conventional processes, this technology is presented in Figure 5.
Figure 5 – Block Diagram for the Alkysafe™ Naphtha Alkylation Technology by UOP Company
The Lummus Company also developed with partners a solid catalyst naphtha alkylation process called AlkyClean™, presented in Figure 6.
Figure 6 – Block Diagram for the AlkyClean™ Naphtha Alkylation Technology by Lummus Company
Despite the effectiveness of the naphtha alkylation processes based on strong acids, the large number of incidents and accidents involving these units are leaving governments and regulators to raise the pressure over the refiners relying on these units, despite the significant capital spending, as quoted above there are technical alternatives to produce alkylated naphtha in safer manner.
Conclusion
The catalytic alkylation process is very attractive to countries with high gasoline consumption and there is a great availability of LPG, as the United States. The production of specific fuels like aviation gasoline still depends on the alkylation catalytic units, so the new and safer technologies can be attractive to refiners with significant demand by this derivative.
As previously mentioned, the alkylation process offers an alternative to produce gasoline with high octane number, with low contaminants content and without emission of harmful compounds to human health, as the case of naphtha from catalytic reforming process.
Despite the high capital investment and operational costs associated to the new technologies of catalytic alkylation units, these processes can be very attractive to the refiners which operate in markets where the demand to high-quality gasoline and petrochemical intermediates is high and it’s always to understand that the lower costs of HF units do not compensate the risks of a severe process accident as occurred in PES refineries, in this case, the refining complex was shutting down and the PES company ended his activities and human life was exposed to risks.
References
Encyclopedia of Hydrocarbons (ENI), Volume II – Refining and Petrochemicals (2006).
Factual Update - Fire and Explosions at Philadelphia Energy Solutions Refinery Hydrofluoric Acid Alkylation Unit - U.S. Chemical Safety and Hazard Investigation Board (CSB), 2019.
GARY, J. H.; HANDWERK, G. E. Petroleum Refining – Technology and Economics.4th ed. Marcel Dekker., 2001.
MYERS, R.A. Handbook of Petroleum Refining Processes. 3a ed. McGraw-Hill, 2004.
ROBINSON, P.R.; HSU, C.S. Handbook of Petroleum Technology. 1st ed. Springer, 2017.