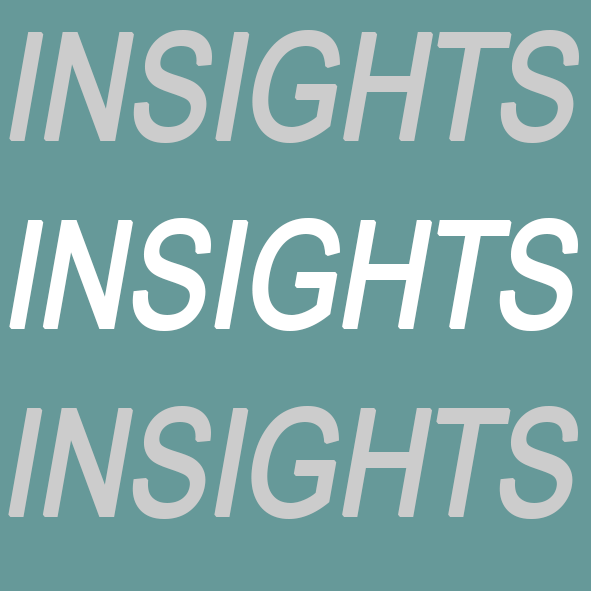
Article
Diolefins Content in the FCC Naphtha and their Impact over the Lifecycle of Hydrotreating Reactors
Introduction and Context
One of the biggest challenges to the crude oil refining industry in the last decades is the development of technologies capable to reduce the environmental impact of the derivatives while raising the performance of these compounds. The hydroprocessing technologies allows the production of cleaner and better performance derivatives at same time that make possible the recovery of higher yields of added value products from bottom barrel streams in the crude oil refining.
The value addition to naphtha streams is especially hard in some cases, mainly to the streams produced by deep conversion processes like Fluid Catalytic Cracking (FCC).
Despite the current trend of reduction of transportation fuels demand, some markets still present great dependence of these crude oil derivatives to sustain his economic development, this is especially true to in development economies like Brazil. The production of high-quality gasoline is still fundamental to refiners aiming to meet the market demand, and considering the current specifications, the synergy between Fluid Catalytic Cracking units (FCC) and Cracked Naphtha Hydrodesulphurization is fundamental to allow the refiners to reach profitable operations, mainly in markets with high demand by transportation fuels.
The North American market is an interesting case study which perfectly describe the challenges of produce low sulfur and high-performance gasoline. Since 2020 the Tier 3 gasoline specifications put under pressure the USA refiners once imposes a maximum sulfur content in the gasoline of 10 ppm at same time which requires better performance (high octane numbers), in practice these restrictions creates more difficulties to the refiners to use their cracked naphtha (Naphtha from FCC) in the gasoline pool once it’s necessary to hydrotreat a higher amount of olefins with octane losses, leading the refiners to look for more selective catalysts and improve their hydroprocessing capacity. Figure 1 presents the evolution of the sulfur content in the USA gasoline market through the years facing the Tier 2 and Tier 3 regulations.
Figure 1 – Average Sulfur Content in USA Gasoline (Hoekstra Trading LLC, 2021)
It’s observed an increasingly reduction in the sulfur content of the gasoline due to the stricter regulation which put under pressure the refiners, especially those which depends exclusively on the cracked naphtha to meet the octane specifications.
Gasoline Production Process
The final gasoline is composed by a blending of different naphtha streams, as presented in Figure 2.
Figure 2 – Example of Process Streams Blending to Produce Gasoline
The use of straight run and reformed naphtha is normally minimized, aiming to direct these streams to petrochemical intermediates market due to the higher added value of these streams in this market.
Cracked naphtha (Naphtha from FCC) contributes positively to the octane number of the final gasoline, however, due to the current restrictions related to the sulfur content in the gasoline (maximum of 10 ppm), the use of cracked naphtha without treatment step is limited. Normally the cracked naphtha is directed to a selective hydrotreating unit aiming to reduce the sulfur content with minimum octane loss, with Tier 3 specifications the severity of the hydrodesulfurization of the cracked naphtha needs to by high leading to a significant raising of octane loss.
Refineries that have catalytic alkylation units in his refining scheme normally direct this stream to produce aviation gasoline that have higher market value when compared with automotive gasoline, for this reason, the participation of the alkylation naphtha is minimized in the composition of this fuel. Despite this, the alkylated naphtha can be an interesting alternative to compose the final gasoline in compliance with Tier 3 regulation once have high octane index and low sulfur content.
Isomerization naphtha has low contaminants content (sulfur and nitrogen) and high-octane number and, for these reasons, the participation of this stream in the formulation of gasoline is maximized in refineries that have isomerization units in the refining scheme. In markets with high demand for gasoline, refiners can add butanes to gasoline pool, however, the participation is limited due to the high vapor pressure of this stream that can lead to break quality requirements (Reid Vapor Pressure – RVP). Normally, butanes are added to LPG pool, respecting the limits to avoid breaking the mixture quality related to heavy limitations.
Nowadays, due to the environmental and quality regulations over the gasoline the hydrodesulphurization of cracked naphtha is fundamental to be possible the refiners meet the sulfur content in the final gasoline that can be low than 10 ppm in most restrictive markets.
FCC Fundamentals
The cracked naphtha is one of the most valuable streams produced in the FCC unit. Typically, the average yield in fluid catalytic cracking units is 55% in volume in cracked naphtha and 30 % in LPG. Figure 3 presents a scheme for the main fractionator of the FCC unit with the principal product streams.
Figure 3 – Main Fractionator Scheme for a Typical Fluid Catalytic Cracking Unit (NICCUM et. al., 2017)
The overhead products from main fractionator are still in gaseous phase and are sent to the gas separation section. The fuel gas is sent to the refinery fuel gas ring, after treatment to remove H2S, where will be burned in fired heaters while the LPG is directed to treatment (MEROX) and further commercialization. The LPG produced by FCC unit have a high content of light olefins (mainly Propylene) so, in some refineries, the LPG stream is processed in a Propylene separation unit to recovery the propylene that has higher added value than LPG.
Cracked naphtha is usually sent to refinery gasoline pool which is formed by naphtha produced by other process units like straight run naphtha, naphtha from the catalytic reforming unit, etc. Due to the production process (deep conversion of residues), the cracked naphtha has high sulfur content and to attend the currently environmental legislation this stream needs to be processed to reducing the contaminants content, mainly sulfur.
The cracked naphtha sulfur removing represents a great technology challenge because is necessary to remove the sulfur components without molecules saturation that gives high octane number for gasoline (mainly olefins).
FCC Naphtha Hydrotreating Technologies
The technology challenge is especially hard to treat the naphtha from Fluid Catalytic Cracking Unit (FCC) dedicated to producing gasoline, one of the most consumed crude derivatives in the world market.
The use of the crude oil increasingly heavier and consequently with higher contaminants content, mainly sulfur, increased further the pressure of the regulatory agents upon the refiners in the sense to reduce the contaminants content in the derivatives, especially Diesel and Gasoline.
Main technology applied to reduce the contaminants content in the crude oil derivatives is the hydrotreating. Figure 4 shows a simplified process scheme for a typical low severity hydrotreating unit.
Figure 4 – Simplified Process Flow Diagram for Typical Low Severity Hydrotreating Units
The process scheme presented in Figure 4 is common and widely applied in the refining industry, however, to produce high-quality gasoline his use is limited once hydrotreating reactions fatally lead to olefins saturation, that are responsible by the high-octane number in the final gasoline. Straight run naphtha is normally directed to conventional hydrotreating as presented in Figure 4 because has a reduced olefin content at the same time which present reduced sulfur content, in this case, the mild hydrotreating process is effective. In the other hand, naphtha from FCC tend to show high sulfur concentration and high olefins content, the processing of this stream in conventional hydrotreating units would be poor effective.
The main chemical reactions associated to cracked naphtha hydrotreating can be represented as follow:
R-CH=CH2 + H2 → R-CH2-CH3 (Olefins Saturation) (1)
R-SH + H2 → R-H + H2S (Hydrodesulfurization) (2)
Where R is a hydrocarbon.
As aforementioned, in the case of naphtha hydrotreating to gasoline, the objective is to minimize the reaction (1) and maximize the yield of the reaction (2), aim to keep the high-octane number while the sulfur content is reduced, making the naphtha more environmentally friendly.
Over the last decades, technology process licensors had devoted his efforts to develop technologies capable to achieve these objectives. UOP Company commercializes the SelectFining™ technology that applies fixed bed reactors to promote a selective hydrotreating of naphtha, lead to the unstable compounds (diolefins) saturation in the first reactor and the heavier olefins (higher sulfur content) saturation in the second reactor using an adequate catalyst.
Nowadays, one of the most applied technologies to reduce the sulfur content in the cracked naphtha is the PRIME G+™ process, developed by the Axens Company. The process applies the concept of which the tendency of the sulfur to concentrate in the heavier fractions of the cracked naphtha, therefore, is carried out a feed stream fractionation before the hydrotreating step, as presented in Figure 5.
Figure 5 – Basic Process Flow Diagram for the PRIME G+ ™ Process by Axens Company
The feed stream is fed to a hydrotreating reactor aim to promote the diolefins saturation, and then the stream is separated in light and heavy fractions in a distillation tower. While the light naphtha is recovered in the top, the heavy fraction is removed from the bottom of the column and sent to a selective hydrotreating section led to a minimum octane lost. In the sequence, the hydrotreated naphtha is separated in a stabilizer column to remove light compounds, the bottom product is mixed with the light fraction and the final product is directed to the refinery gasoline pool.
Another technology that applies selective hydrotreating to reduce the sulfur content in the cracked naphtha is the Scanfinning™ process developed by ExxonMobil Company, in this case, are applied fixed bed reactors without feed stream fractionation. Regarding the catalysts dedicated to selective hydrogenation of FCC naphtha, we can highlight the product HyOctane™ developed by Haldor Topsoe company.
The GT-DeSulph™ process developed by Sulzer-GTC Engineering Company applies the extractive distillation principle associated with selective hydrotreating, the use of aromatics solvents allows remove thiophenic compounds from cracked naphtha.
Another interesting route adopted by the licensors is the non-selective hydrotreating followed by an octane index recovery step, the ISAL™ technology by UOP Company employs this principle. In this case, through an adequate catalyst, occurs the olefins saturation and posteriorly is carried out the molecular rearrangement to recover the octane index lost in the first step.
The S-Zorb™ process developed by ConocoPhillips applies the concept of chemical adsorption of the sulfur compounds on zinc oxide (ZnO) and has a continuous regeneration system of the adsorbent through controlled burn of the adsorbed sulfur compounds. Another attractive technology applied to FCC naphtha desulfurization is the CDHydro + CDHDS™ process commercialized by Lummus company which is based on reactive distillation and hydrodesulfurization as presented in Figure 6.
Figure 6 – Basic Process Flow Diagram for CDHydro + CDHDS™ Technology (HA & MERCER, 2018)
FCC naphtha is a fundamental stream for the refiners to meet the automotive gasoline requirements (minimum octane number), and the adequate treatment of this process stream is necessary to ensure the adherence to environmental regulations at same time in raise the profitability of the refiner once the cracked naphtha yield in the fluid catalytic cracking units can reach over than 50 %, as aforementioned.
It's important to remember that the main objective of the Selective Hydrotreating Unit (SHU) is to control the contaminants content to the hydrodesulfurization section, especially polymers and gum precursors like diolefins which tends to produce coke in the catalyst pores, leading to quick deactivation and pressure drop in the catalytic bed.
A Special Challenge – Dienes (Diolefins) Control
A key parameter in the cracked naphtha is the conjugated dienes content, these compounds are chemically unstable and tend to suffer oxidation reactions leading to gum formation in the reactors in hydrodesulphurization units, leading to high pressure drop and lower operation campaigns.
The dienes formation in fluid catalytic cracking units occurs mainly in the transfer line between the reaction section and the fractionator or in the final section of the riser. This phenomenon is caused by the absence of catalyst in this section and, due to the high temperature, the thermal cracking occurs, favoring the dienes production. In well-designed FCC reactors, the temperature in the riser falls quickly maximizing the catalytic reactions and minimizing the thermal cracking reactions, as presented in Figure 7.
Figure 7 – Effects of the FCC Feed Nozzle Design Over the Thermal Cracking Occurrence (LETSZCH et. al., 2009)
Due to these characteristics, the refiners normally control the dienes production through the quench injection in some point of post riser aiming to reduce the temperature, avoiding then the thermal cracking and dienes formation. The literature quotes that is possible to reduce close to 50 % of the dienes formation applying post riser quench with light cycle oil (LCO). The main process licensors recommend the quench injection in the separator vessel (diluted phase) once the injection in the transfer line can lead to hydrocarbon condensation and coke deposition in the bottom of main fractionator, the use of quench in the riser tends to raise the production of fuel gas and coke which can limit the FCC units in the machines like blower and cold area compressors. Figure 7 presents a process flow diagram for the R2R™ FCC technology commercialized by Axens company.
Figure 8 – R2R™ FCC Technology by Axens Relying on Post Riser Quench Devices
The quench injection in the post riser section is even more important to FCC units operating under high severity, where the operating conditions favors the dienes formation in higher rates (higher temperature in the post riser sections).
The dienes concentration in the cracked naphtha is normally controlled through the Maleic Anhydride Value (MAV) that is defined by a quantity of Maleic Anhydride (in mg) necessary to react with one gram of cracked naphtha through Diels-Alder mechanism as presented in Figure 9.
Figure 9 – Diels-Alder Reaction for a Conjugated Diene (SOLOMONS et. al., 2018)
Some refiners usually control the MAV below of 4,0 mg/g, but it’s important consider that the dienes concentration is not the unique parameter to keep a reliable operation in the cracked naphtha hydrodesulphurization unit. Control the concentration of light compounds in the feed (C4) is important to avoid sudden vaporization in the catalyst bed, leading to lower reaction temperatures in the selective hydrogenation unit that cause lower conversion consequently raising the diolefins (dienes) concentration in the main reaction section that can lead to gum formation, reducing the operation lifecycle. The lights concentration in the cracked naphtha is controlled through the Reid Vapor Pressure, another side effect of the diolefins concentration in FCC naphtha hydrotreaters is related to the polymerization in the catalyst bed leading to higher pressure drop and shorter operating lifecycle.
Face to the current specifications of gasoline, the cracked naphtha hydrodesulphurization unit became fundamental to allow refiners relying on FCC units in his refining scheme to produce marketable gasoline. An unplanned shutdown of this unit can quickly lead to a FCC shutdown and, in extreme cases, the interruption of refinery operations.
In some cases, can be observed premature activity loss in the Selective Hydrotreating Unit (SHU), this scenario can be overcome through lower temperature in the FCC unit (TRX) which can be compensate through a high activity of the FCC catalyst.
It’s important to consider that the matter with dienes in the cracked naphtha tends to raise with the operating severity of the fluid catalytic cracking unit. In the last years we are seeing a trend among the refiners aiming to revamp their FCC units focusing in to improve the olefins throughput which can intensify the problems with dienes content in the cracked naphtha. It’s important to consider the possibility to include a quench stream in the post riser section to control this parameter in the cracked naphtha and preserve the health of hydrodesulfurization reactors.
Controlling the Pressure Drop - Guard Beds against Contaminants
Control the catalyst lifecycle is a key issue to refiners, especially in FCC naphtha hydrodesulfurization units, and one of the main strategies adopted in the last years is the use of guard beds in hydroprocessing catalysts to protect the catalysts, ensuring longer and most profitable operating campaign.
The main objective of the guard bed is to protect the main and active catalyst against:
- Particulates from the feedstock that can be dragged like sediments, catalysts powder and corrosion products that are capable to produce physical fouling;
- Heavier hydrocarbons capable to lead of coking deposition;
- Chemical unstable hydrocarbons capable to produce gum, like olefins and diolefins;
- Metals and catalysts poisons like Ni, V, Fe, Si, Na, etc.
As aforementioned, due to the higher concentration of contaminants the guard beds are most common in hydroprocessing units dedicated to processing heavier feedstocks, as quoted above. Normally is applied a grading strategy in the catalyst bed aiming to establish a staggering of pore diameter and activity to the catalysts, keeping the catalysts in the top more resistant to the contaminants acting as a filter, protecting then the most active catalyst in the bottom section, Figure 10 presents an example of hydroprocessing catalysts grading according to STAX™ technology by Albemarle Company.
Figure 10 – Example of Hydroprocessing Catalyts Grading (LELIVELD & TOSHIMA, 2015)
In Figure 10, the guard bed will be responsible to control the contaminants content (mainly metals) to the next catalyst sections as well as to reduce the carbon residue (CCR) and particulates concentration, keeping the activity and improving the lifecycle of the hydroprocessing unit.
Among the most known catalyst protection technologies available in the market, we can quote the CatTrap™ technology developed by Crystaphase Company, this technology applies a ceramic bed acting as a filter to particulate materials, controlling especially the pressure drop in the catalyst bed.
For units dedicated to treat bottom barrel streams, the hydroprocessing catalyst needs present high activity and be resistant to the high contaminants content (sulfur, nitrogen, and silicon), some companies have been dedicated his efforts to develop catalytic systems capable to attend these requirements, as examples of these technologies we can quote the START™ system by Advanced Refining Technologies (ART) Company, the UNITY™ system developed by UOP Company, the SENTRY™ catalysts by Criterion Catalysts Company, and the TK-449 Silicon Trap™ by Haldor Topsoe Company. Figure 11 presents a comparative study developed by Haldor Topsoe Company related to the improvement of the cycle length of a naphtha hydrotreating unit applying grading particles to control the contaminants content over the main catalyst.
Figure 11 – Cycle Length Improvement in a Naphtha Hydrotreating Unit with Catalyst Grading (Haldor Topsoe Company, 2020)
The increasing relevance of the hydroprocessing technologies to the downstream industry requires even more attention from refineries aiming to keep profitable and reliable operations in these units, the guard beds technologies have an important role to allow the achievement of this goal, as presented in Figure 11 these technologies can improve in a significant manner the operational lifecycle of the hydroprocessing units.
Conclusion
Despite the recent forecasts, the transportation fuels demand responds by great part of revenues in the downstream market, especially in developing economies. The capacity to add value to the naphtha from catalytic cracking processes like FCC is fundamental not only to ensure better profitability to refiners but also the minimize the environmental footprint in the crude oil processing chain.
As aforementioned an integrated operation between FCC and Cracked Naphtha Hydrodesulphurization units is fundamental to the refiners achieve profitable, reliable, and competitive operations in the downstream market and, as presented above the dienes control in the FCC naphtha is a key topic which need especial attention from the refiners, according to the refining scheme the unavailability of the cracked naphtha desulfurization unit can make unfeasible the operation of the whole refinery.
This topic became especial relevant in the last years due to the announce of the Tier 3 regulation in the USA market (a great gasoline consumer market) which limit the sulfur content in the final gasoline in 10 ppm, creating additional challenges to refiners to meet this requirement, especially for those refiners which depends on FCC naphtha to compose their gasoline pool.
References
HA, H. Z.; MERCER, D. B. Dynamic column simulation delivers reduced relief load. PTQ Magazine, 2018.
HOEKSTRA, G. Gasoline Desulfurization for Tier 3 Compliance. 1st ed. Lulu press, 2020.
ITO, E.; VEEN, R.V. On Novel Processes for Removing Sulphur from Refinery Streams. Catalysis Today 116 (2006) pp. 446-460 – Elsevier.
LELIVELD, B.; TOSHIMA, H. Hydrotreating Challenges and Opportunities with Tight Oil. PTQ Magazine, 2015.
LETZSCH, W.; SANTNER, C.; TRAGESSER, S. FCC Reactor Design – Part II. PTQ Magazine, 2009.
MYERS, R.A. Handbook of Petroleum Refining Processes. 3a ed. McGraw-Hill, 2004.
NICCUM, P.; McDANIEL, W.; POLLICOFF, H. FCC Product Fractionation for Maximum LCO, PTQ Magazine, 2017.
QUINN, G. P.; SILVERMAN, M. A. Post Riser Quench Improves FCC Unit Profitability. Oil & Gas Journal, 1996.
ROBINSON, P.R.; HSU, C.S. Handbook of Petroleum Technology. 1a ed. Springer, 2017.
ZHU, F.; HOEHN, R.; THAKKAR, V.; YUH, E. Hydroprocessing for Clean Energy – Design, Operation, and Optimization. 1st ed. Wiley Press, 2017.