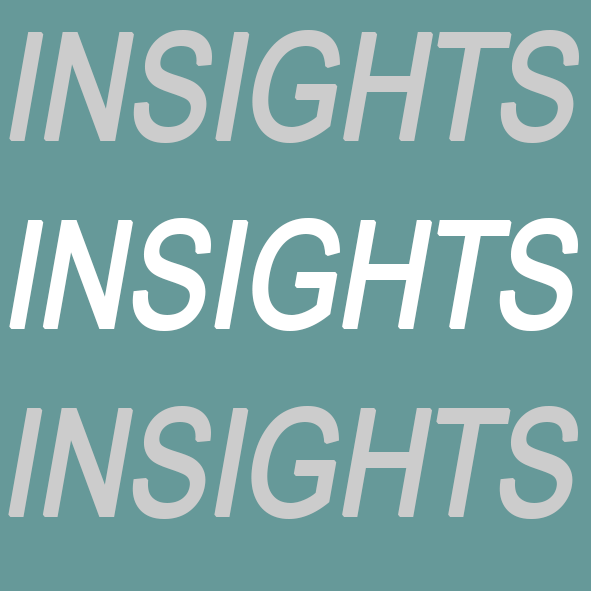
Article
Lump Kinetic Modeling for Refinery Reactions using HYSYS Refinery and Aspen Custom Modeler
Introduction:
Operating a refinery under turn down conditions is a critical undertaking, primarily because the operating parameters can deviate from the ideal operational range. Properly addressing turn down operation is essential to prevent operational disruptions and extend the lifespan of catalysts.
For instance, consider a Naphtha hydrodesulfurization complex unit designed to handle an inlet feed rate of 17,230 barrels per day (bbl/d) for Naphtha. Unfortunately, in this particular case, both the licensor and the engineering, procurement, and construction (EPC) team did not give due consideration to the turn down ratio, which should have been at least 45%.
To address this issue, we employed fundamental principles of chemical reactions. We began by constructing a kinetic model, utilizing reactor information provided by the licensor and a comprehensive thermodynamic database to identify the Gibbs free energy (ΔG) and entropy associated with several key reactions:
- Mercaptan + H2 ↔ CH4 + H2S
- Thiophene + 4H2 ↔ C4H10 + H2S
- Dibenzothiophene + 2H2 ↔ Diphenyl + H2S
The assessment roadmap outlined below was effectively implemented for the 100% design case, yielding results that closely aligned with the licensor's provided kinetics. For anyone interested in conducting a similar assessment, I would highly recommend following this roadmap:
-
Data Collection and Review: Begin by gathering all relevant data, including reactor information and component thermodynamic data.
-
Kinetic Model Development: Construct a kinetic model based on the available data and reactions of interest.
-
Reaction Thermodynamics: Utilize the thermodynamic data to determine the Gibbs free energy (ΔG) and entropy associated with the chosen reactions.
-
Assessment and Calibration: Assess the model's performance against the available data, and calibrate it as needed to achieve accurate predictions.
-
Regression Analysis: Perform various regression analyses to fine-tune the kinetic model, ensuring it aligns closely with the licensor's provided kinetics.
By following this systematic roadmap, you can effectively address turn down operation challenges and optimize the performance of complex units in the refining industry.
Technical Discussion
Within HYSYS, each component can generate a polynomial equation to calculate the Gibbs energy at any given temperature. This information is then managed by an Excel VBA (Visual Basic for Applications) script. The VBA script ensures that the equations, and by extension, the reactions, are balanced. It then calculates the equilibrium constant, K, using the equation dG = -RT ln(K), where R is the gas constant, T is the temperature, and ln denotes the natural logarithm. Given the reaction pressure and temperature, the partial pressures (PP) are determined as a function of conversion, pressure (P), and temperature (T). The K value is then calculated.
Automated goal-seeking processes within VBA ensure that the K value calculated from Gibbs energy equals the K value derived from partial pressures by manipulating the conversion.
The Arrhenius equation is derived from the data obtained above, taking the form: K = A * exp(-E/RT), where A is the Arrhenius factor, E is the activation energy, R is the gas constant, and T is the temperature. This equation describes the temperature dependency of the equilibrium constant.
For solving the rate equation of Naphtha hydrodesulfurization (HDS), key Ordinary Differential Equations (ODEs) and auxiliary equations are identified. Specifically, the rate of change of concentration with respect to temperature (dC/dT) is described by the equation dC/dT = -K * C^n, where K is the rate constant, C is the concentration, and n is a reaction order.
To provide context, initial and final sulfur content levels, as well as the catalyst's liquid space hourly velocity (LSHV), are specified. Further tuning is applied to the Arrhenius factor (A) and the activation energy (E/R). These adjustments result in a close match to the base case, allowing the process to run effectively at a temperature of 280°C.
Additionally, it's noted that altering the flow rate to 45% of its original value while maintaining the same catalyst volume will require an increase in the liquid space hourly velocity (LSHV). Introducing a lower flow rate at the same temperature will lead to higher sulfur content in the product. This detailed process ensures precise control and optimization of the hydrodesulfurization reaction in the Naphtha unit.
The 45% of the flow rate to the same catalyst volume would need more LSHV (Liquid Space Hourly Velocity), and the introduction of lower flow at the same temperature will result in a higher sulfur content.
Re-running the model using the TDR flow, has resulted in a high sulfur content of 0.2 wt% at outlet which is not accepted due to the purity agreement of Light Naphtha and Heavy Naphtha to the local market. Engaging the Optimization tool in Aspen Custom Modeler has reported a feed temperature of 465°C for the TDR to meet the sulfur content.
Conclusion
In conclusion, the hydrogenation reaction within the Naphtha hydrodesulfurization process exhibits a temperature-dependent behavior. At higher temperatures, the reaction is favored, leading to higher conversion rates, while at lower temperatures, it tends to reverse, causing the reformation of hydrogen sulfide (H2S) into sulfur.
In our role as consultants, we conducted a comprehensive examination of the reaction conditions, specifically focusing on the operating temperature of 265°C. This temperature was found to be well-suited for the reaction, as it maintained an exceptionally high conversion rate, with a minimal drop from 99.6% to 99.45%. This level of conversion is not only acceptable but also indicative of the effective control and optimization of the hydrogenation process within the Naphtha hydrodesulfurization unit.
The software tools utilized throughout this assessment were Aspen HYSYS, which provided valuable insights into the process, Excel-based VBA scripts, and Aspen Custom Modeler, enabling precise modeling and calculations to support our analysis. These software resources played a crucial role in ensuring the accuracy and reliability of our findings, ultimately contributing to the successful assessment of the Naphtha hydrodesulfurization process.
#refining #refinery #processsimulation #naphtha #HYSYS #AspenCustomModeler #OptimizeSolutions #Consulting #Oil&Gas
Braun, Uwe
10/3/2023 12:40 PM
Thank you Emad. Very interesting Article. We would be happy to link it with Refineries, where this is applicable. |