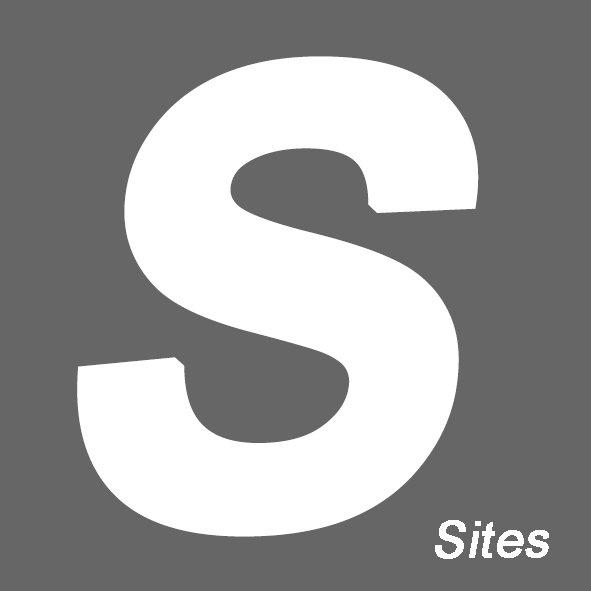
Site Message
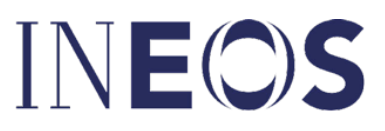
Ethane Cracker - Detailed Description
- Site
- Project One - Ethane Cracker Project
- Message Category
-
Portfolio and Mass Balance Information
From INEOS, Project ONE, Environmental & Social Impact Assessment (ESIA).
General
The ethane cracker (ECR) is located in the southern part of the project area and is one of the most innovative, efficient and sustainable cracking facilities in the world. The ethane cracker will have a production capacity of 1 450 000 tonnes/year of ethylene.
If there is a shortage of ethane as a feedstock in the short term, propane can be partially used as a backup feedstock - in fact, the ECR can be fed with a mixture of about 20% propane and 80% ethane.
The main components of the ECR are:
• Main units:
• an oven section;
• a water quench and dilution steam production;
• a compression and alkaline treatment;
• the partition.
• Additional support units: steam and condensate, slop and waste water system.
In the separation section of the ECR, in addition to pure ethylene, other fractions including pure propylene are obtained. It will also be possible to add externally supplied propylene to the separation section. This concerns so-called chemical grade propylene with a lower degree of purity than the polymer grade propylene that is obtained at Project One. The chemical grade propylene is further purified in this way to polymer grade propylene, with the impurities being removed and ending up in other fractions. Project One plans to produce 230 500 tonnes/year of pure (polymer grade) propylene in this way.
Oven Section
The ethane is mixed with dilution steam and an ethane-rich recycle stream to obtain a suitable reaction mixture. This is passed in parallel through the furnaces.
The furnace section consists of 6 parallel furnaces. They are arranged in 3 pairs, each pair consisting of two mirrored ovens placed 'back to back'. The operation and capacity of the 6 ovens is otherwise identical. Each oven consists of a radiation section and a convection section. In the radiation section, the conversion of ethane to ethylene and by-products (high value chemicals) takes place. The reactions take place at high temperatures in tube reactors (coils). The high temperatures are achieved by burning fuel gas in burners. In order to minimize fuel consumption, the suctioned air is preheated with residual heat.
Over time, coke deposits form on the inside of these coils. The formation of this coke is slowed down as much as possible by, among other things, using suitable coil material, diluting the hydrocarbon reaction mixture with steam, and adding sulphur components to the reaction mixture, but it cannot be avoided completely. These cokes form an insulating layer on the inside of the coils. When this insulation layer becomes too thick, the wall temperature of these coils approaches its structural limit and the coke layer must be removed.
When the reaction mixture leaves the coils, it is cooled as quickly as possible to prevent further reaction. This is done in heat exchangers that produce high-pressure steam from the exchanged heat.
In the convection section, the flue gas produced by the combustion of the fuel in the burners is conveyed to the chimney by means of a succession of heat exchangers and an electrically driven fan. This section is designed to recover the maximum amount of residual heat in the gas.
Water quench and dilution steam production
In the water quench section, the residual heat from the process gas, which cannot be converted to steam, is removed by direct contact with process water. This causes the dilution steam present in the reaction mixture to be condensed together with the heavier hydrocarbon components (C5+ fraction and pyrolysis oil), after which the oil phase is separated from the water phase in a liquid-liquid separator. Coke and tar are also purified from the reaction mixture in this section. The process water is further used to produce process steam (dilution steam).
Compression and alkaline treatment
In the compression section, the process gas is compressed to the pressure required for further product separation.
In the alkaline treatment, acid gases (H2S, CO2, etc.) from the process gas are neutralised and removed with NaOH (sodium hydroxide). A specific wastewater flow is created (so-called 'spent caustic') containing the acidic components and a surplus of NaOH. This wastewater flow is given a separate pre-treatment in the water purification system.
Separation
In the separation section, the process gas is separated into its various components which are then purified into products that meet set specifications, primarily by distillation. First, the process gas is further cooled and dried. Then, all components with two or less carbon atoms are separated from those with at least three carbon atoms. The stream with two or less carbon atoms contains the component acetylene, which is reacted to ethylene in the C2-hydrogenation. This stream is then cooled down very strongly. At these low temperatures, the fuel gas (mixture of mainly methane and hydrogen) can be separated from the components with two carbon atoms. The remaining tail gas is sent as fuel gas to the furnaces and steam boilers to be burned. The stream with two carbon atoms is a mixture of ethane and ethylene. These two components are then separated from each other. Ethylene is delivered as an end product to the boundary of the ethane cracker. Ethane is sent back to the furnaces as a recycle stream as feed.
From the stream with at least three carbon atoms, first the components with exactly three carbon atoms are extracted. This mixture consists mainly of propane and propylene. A small part of di-olefins can also be found in the mixture. These are hydrogenated in the C3 hydrogenation. This C3 mixture stream is combined with imported chemical grade propylene. This is less pure propylene (approximately 95% pure), which still contains other hydrocarbons. The mixed flow is then sent to the C3-splitter for further purification. In the C3 splitter, propylene on the one hand and propane and other hydrocarbons on the other are separated.
Propane can be returned to the furnaces. The propylene is obtained in a very pure form (polymer grade propylene, approx. 99.5% pure) and is discharged via pipelines as one of the end products of the cracker.
After the separation of the components with 3 carbon atoms, a mixture of components with at least 4 carbon atoms remains. As a final step, this mixture is split into a C4 mixture and a C5+ mixture. These flows are stored and disposed of, also as end products.