Site

-
- Repsol Tarragona Refinery
-
- Repsol S.A.
- Site Category
- Refining and Chemicals Operations
- Location
- Street
- Poligono Industrial
- Additional Location Info
- 43140 La Pon;a de Mafumet
- Website
- Description
-
Interactive map of installations of Repsol Tarragona manufacturing location on Respol website. (accessed 19th Mar 2025)Complex's Marine Terminal
"El Pantalán", Repsol's marine terminal, includes five berthing bays for unloading oil tankers, and a single-moor mooring located three kilometers from the coast where supertankers can unload their contents.
Energy Generation
- The cogeneration plant provides part of the thermal and electrical energy we need for our operations, using natural gas as fuel.
- Electric energy park: Repsol has launched its Repsol Electricidad y Gas brand in Spain, making the company a significant player in the Spanish electricity market, with more than 2,952 MW of total installed capacity.
Refining
The refining complex houses all the production units used to process crude oil and distill it, thus obtaining numerous derivatives for processing. The entire area processes a total of 9,500,000 tons of raw material per year. This area includes:
- Tank farm with a combined storage tank capacity of one million cubic meters. The crude oil arriving at the refinery is stored in these tanks until it is processed in the atmospheric distillation units. Before processing, any water that may be present in the crude oil is removed.
- Crude oil distillation unit (CDU), both ADU and VDU. The VDU produces two cuts: vacuum diesel and vacuum residue.
- Hydrotreatment plants removing sulfur from the ADU products through a chemical reaction with hydrogen. The sulfur extracted in the gas phase solidifies, allowing it to be marketed as a final product.
- Mild-Hydrocracker processing the vacuum diesel from the VDU.
- Coker unit processing the residue from the VDU.
- Hydrocracker converting low value products into high-quality fuels, such as naphtha (gasoline, diesel, and kerosene.
- Fuel blending plant: the complex's various plants generate streams that will become part of the final blend of LPG, kerosene, gasoline, diesel, and other commercial products. The blending area includes both the product transfer lines and pipelines, as well as pumping systems and tank farms for storage. Additives are also added to the final blend to optimize its properties.
Environmental and Safety Devices
- Through the chimneys, the combustion gases from the refining process that cannot be recovered are safely and controlledly expelled. The central chimney is a more than 100-meter high tower.
- Torches are continuously and in a controlled manner burning the easily evaporable fluids and gases processed in the industrial complex into flares.
- The VOC (Volatile Organic Compound) removal plant filters all effluent sent to the wastewater treatment plant.
- The waste water treatment plant recyclies almost all the water used by the site.
Chemicals
The chemical area of the complex is responsible for transforming the olefins obtained during refining into various polymers, including
the following plants and units:- Methyl methacrylate plant.
- Olefins plants with a production capacity of 650,000 tons of ethylene, 380,000 tons of propylene, also producing butadiene and benzene.
- Four polyolefin plants, with a combined capacity of 690,000 tons of polyethylene and polypropylene:
- The Low Density Polyethylene (LDPE) production process is a continuous, high-pressure autoclave process in which the ethylene enters the reactor at a pressure range of 1300–1600 kg/cm2.
- The High Density Polyethylene plant (HDPE) produces ethylene homopolymers and copolymers with a chromium catalyst, with densities between 0.940 and 0.960 g/cm3 and a wide range of melt flow rates. Since 2016, ethylene copolymers have been produced with a metallocene catalyst. In both cases, the process involves the polymerization of ethylene with 1-hexene as the copolymer and isobutane as the reaction medium.
- During the last quarter of 2016, the construction of the second phase of construction of the metallocene polyethylene unit began by employing Chevron Phillips Chemical MarTECH SL Loop Slurry Technology, Repsol becoming the first unit to produce metallocen PE outside the United States. The plant produces both metallocene linear low density polyethylene (mLDPE) and high-density polyethylene (HDPE). This mLLDPE plant is designed to share some critical facilities and equipment with the existing HDPE unit.
- The polypropylene plant produces polymers by the polymerization of propylene monomers taking place in two loop reactors operating in series under the same pressure and temperature conditions. In addition to the prepolymer and liquid propylene streams, the reactors are also fed a hydrogen stream, which is very important for controlling the melt flow rate.
- Butadiene plant obtaining butadiene from the steam cracking C4 fraction.
- Glycol plant producing propylene glycols by reacting propylene oxide with process water. The reactor effluent is concentrated in the evaporation section, recovering the unreacted water. The glycols are then fed to a distillation system where the various types of glycols are obtained.
- Three polyol plants converting propylene glycol and ethylene glycol into approximately 200,000 tons of different types of polyols.
- The ethylbenzene plant produces ethylbenzene by the alkyation reaction of benzene with ethylene.
- The propylene oxide / styrene monomer (PO/SM) plant converts ethylbenzene by oxidation with air and the resulting product is fed to the epoxidation unit to obtain crude propylene oxide and methyl benzyl alcohol. In other units of this plant, the propylene oxide is purified and the methyl benzyl alcohol is dehydrated to obtain styrene.
LPG
The liquefied petroleum gas (LPG) treatment plant produces approximately 482,000 tons of LPG annually. The plant's activity consists of receiving LPG, usually imported, by sea, as well as its storage and subsequent delivery. Currently, this section of the complex is responsible for supplying butane, propane, and other liquefiable gases to the entire northeast quadrant of the peninsula.
System Info
- Modified by
-
Kokel, Nicolas
- Modified
- 3/19/2025 7:25 AM
- Added by
-
Braun (Sysadmin), Uwe
- Added
- 3/13/2022 6:15 PM

No Services yet available. Go to Solutions to enquire how we can help you or how you can market your own expertise.
Enquire in Solutions how we can help you.
Dashboard
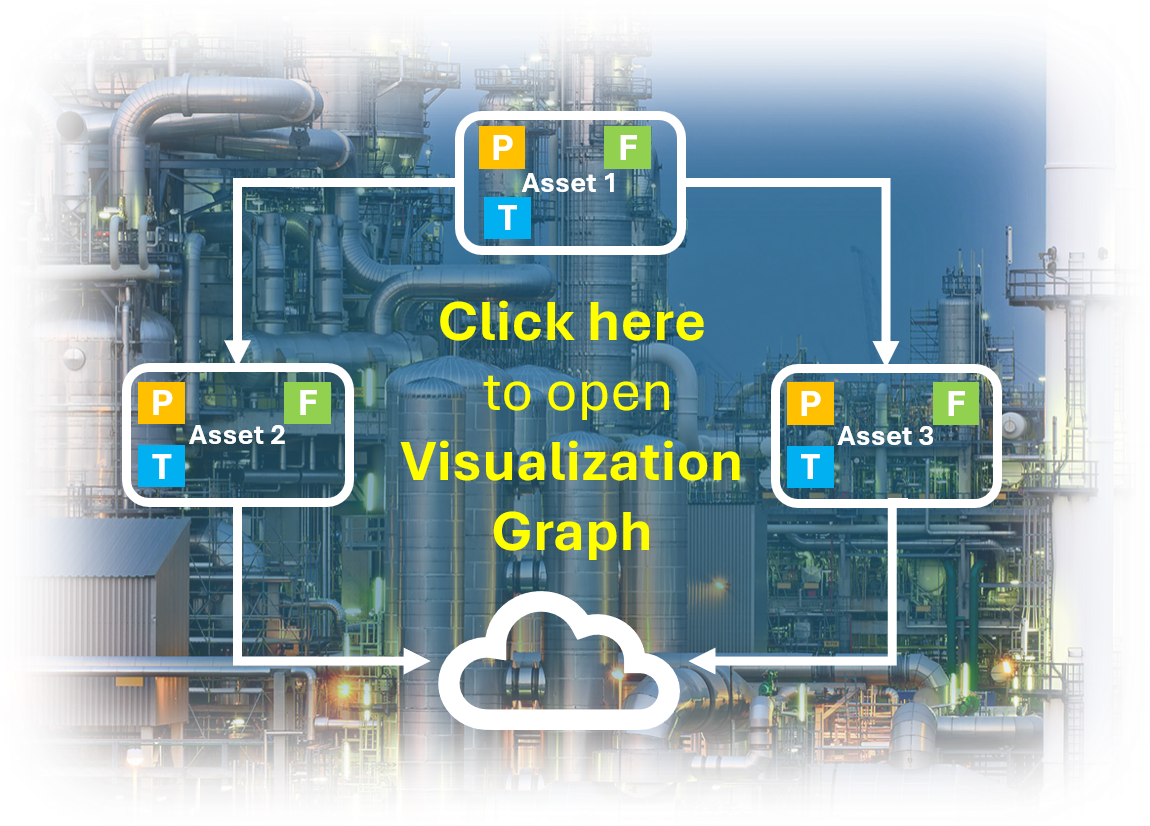