ppPLUS: Technologies and more
Go to Homepage to browse companies and process data
ppPLUS-Solutions providing Services and Support
Register creating your own models
Technology
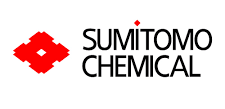
- Name
- Sumitomo MMA
- Owner
-
/ Sumitomo Chemical Company, Limited
- Brand
- MMA Process
- Process
- Oxidation
- Type
- Isobutylene Oxidation
- Available
- Description
-
Technology Summary
The Sumitomo's methyl methacrylate (MMA) process is a tandem method for direct oxidation in two steps of isobutene into methacrylic acid via the intermediate methacrolein (MAL). In this tandem method the gas generated in the first stage is supplied directly to the second step. The heart of the direct oxidation process is the catalytic two-step oxidation reaction.
Technology History
Sumitomo Chemical has commercialized a direct isobutylene oxidation method in cooperation with Nippon Shokubai Co., Ltd. as advertized in 1992. By 2004, the Sumitomo Chemical / Nippon Shokubai technology has expanded to five plants, including plants in Korea and Singapore, and another plant was being constructed. The history of Sumitomo Chemical’s MMA operations until 2005 is as follows:
- 1962: Starting to research on C4 direct oxidation;
- 1964: Introduction of SOHIO acrylonitrile (Niihama);
- 1967: Introduction of MMA polymer (Sumipex) from ICI;
- 1967: Start-up of production of monomer-MMA (ACH process);
- 1982: Semi-commercial C4 Direct Oxidation by Nippon Shokubai (Himeji);
- 1982: Foundation of Japan Methacryl Monomer (J/V with Nippon Shokubai);
- 1984: Start-up of JMM Niihama plant;
- 1989: Start-up of JMM Himeji plant;
- 1993: Start-up of LGMMA plant (Korea);
- 1998: Start-up of SMM plant (Singapore);
- 2002: Business exchange of Acrylic Acid and MMA with Nippon Shokubai;
- 2003: Start-up of LGMMA 2nd plant;
- 2005: Scheduled start-up of SMM 2nd plan.
Technology Description
The Sumitomo Chemical / Nippon Shokubai MMA production method is a two-step direct oxidation process of isobutylene into methacrylic acid via intermediate methacrolein followed by esterification of methacrylic acid with methanol into MMA as per the following chemical equation:
High-purity isobutylene is generally obtained by the MTBE backcracking process.
The gas generated in the first stage is supplied directly to the second step in the tandem method, so the unreacted isobutylene and high boiling point byproducts are brought to the second step without alteration. Since isobutylene, in particular, inhibits the second step reaction, the first step conversion must be as high as possible. Since the reaction in the second step is inhibited by isobutylene and the byproducts, and there is a limit to the methacrolein concentration, a large reaction vessel is necessary for the tandem method.
The requirements for catalyst performance can be said to be strict, but the problem has been solved by Sumitomo Chemical / Nippon Shokubai using a first step catalyst that has an extremely high conversion rate without lowering the yield, and a tough, long-life second step catalyst that exhibits sufficient capacity even in the presence of poisonous materials.
The first step catalyst is a Mo-Bi multi component composite oxide catalyst ( Mo-Bi-Fe-Co/Ni-A (A: alkali metal, alkaline earth, Tl) composite oxide) similar to that for propylene oxidation. In contrast, the catalyst developed for the second step is a PMo heteropolyacid catalyst (heteropolyacid with an anion structure known as the Keggin structure of [PMo12O40]3–) with a structure that differs from the Mo-V catalyst for acrolein oxidation.
As of 2004, Sumitomo Chemical was continuing to be put efforts nto improving the performance of the second step catalyst, which performance is aknowledged to be not statisfactory.
At this stage of process development, isobutene conversion is 100% and MMA yield is 65%. Unit consumptions are mentioned to be:
- 0.86 tonne Isobutene per tonne MMA;
- 500 kWh per tonne MMA;
- -1 tonne Steam per tonne MMA.
Process Block Flow Diagram
The simplified process diagram is presented in the attached illustration, which shows that essential units are two reactors in series, a scrubber, an adsorber and a stripper.
References
- Koichi N AGAI, Toshiaki U I, SUMITOMO KAGAKU (English Edition) 2004-II, Report 1, Trends and Future of Monomer-MMA Technologies.
- Link
System Info
- Updated by
-
Kokel, Nicolas
- Updated
- 12/30/2024 10:32 AM
- Added by
-
Kokel, Nicolas
- Added
- 1/12/2021 12:13 PM

No Services yet available.
Go to Solutions to enquire how we can help you or how you can market your own expertise.
Enquire in Solutions how we can help you.