ppPLUS: Technologies and more
Go to Homepage to browse companies and process data
ppPLUS-Solutions providing Services and Support
Register creating your own models
Technology
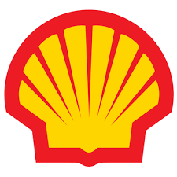
- Name
- Shell Hycon MB
- Owner
-
/ Shell PLC
- Brand
- Hycon Moving Bed Technology
- Process
- Cracking
- Type
- Resid Hydrocracking
- Available
- Description
-
With High-Metals Feedstocks, even Hydrodemetallization (HDM) Catalysts have a relatively short life, so frequent Catalyst replenishment is necessary. In the Shell Hycon MB Process, Fresh Catalyst is semi-continuously added at the Top of the Reactor while Spent Catalyst is withdrawn from the Bottom. In this way, the Catalysts are constantly replenished and have a consistent, high activity level with no real deactivation over time. Furthermore, this enables a relatively large volume of Demetallisation Catalyst to be used; essentially, the Shell Hycon MB Technology enables the Catalyst activity of a large array of Fixed Bed HDM Reactors to be achieved in one or two Moving Bed Teactors, but without the resultant large pressure drop and consequent penalties on Reactor Hydraulics and Hydrogen partial pressure. The Rate of Catalyst Replenishment is controlled in accordance with the rate of Metal Deposition. Special Screens separate the Catalysts from the Process Fluids before they leave the Reactor. The Shell Hycon MB Reactors operate in trickle flow to ensure the highest flow stability and the best Reaction and temperature control. This also maximises the temperature operating window. Each Moving Bed reactor is equipped with proprietary Internals that optimise the distribution of Fluid throughout the Reactor while also allowing Catalyst flow during replenishment. Underutilised Spent Catalyst can be recycled back into the System so that Catalyst fill costs can be optimised and the overall Catalyst Activity remains at a constant level.
Some of the Benefits of the Shell Hycon MB Technology are:- Increased Crude Flexibility compared with Fixed-Bed Technology, unlocking the use of High-Metals Crudes and High-Metal Feeds such as Resids and DAO.
- Reduced Fuel Oil Production due to the ability to process Vacuum Resid Feedstock that would otherwise be routed to Fue Oil Pool.
- Increased Middle Distillate Yield by decoupling Contaminant Removal, mainly Metals such as Vanadium and Nickel, from High-Value Hydroprocessing System.
- Increased Upgrading of Crude Barrels and Vacuum Residues to Naphtha for Petrochemicals, thereby supporting Crude-to-Chemicals targets.
- Extended Cycle Length by reducing the Contaminants Load (total Metals Deposition) on the Catalyst in the Downstream Fixed Bed Reactors.
- Link
System Info
- Updated by
-
Kokel, Nicolas
- Updated
- 11/20/2022 7:16 PM
- Added by
-
Kokel, Nicolas
- Added
- 11/20/2022 4:35 PM

No Services yet available.
Go to Solutions to enquire how we can help you or how you can market your own expertise.
Enquire in Solutions how we can help you.