ppPLUS: Technologies and more
Go to Homepage to browse companies and process data
ppPLUS-Solutions providing Services and Support
Register creating your own models
Technology
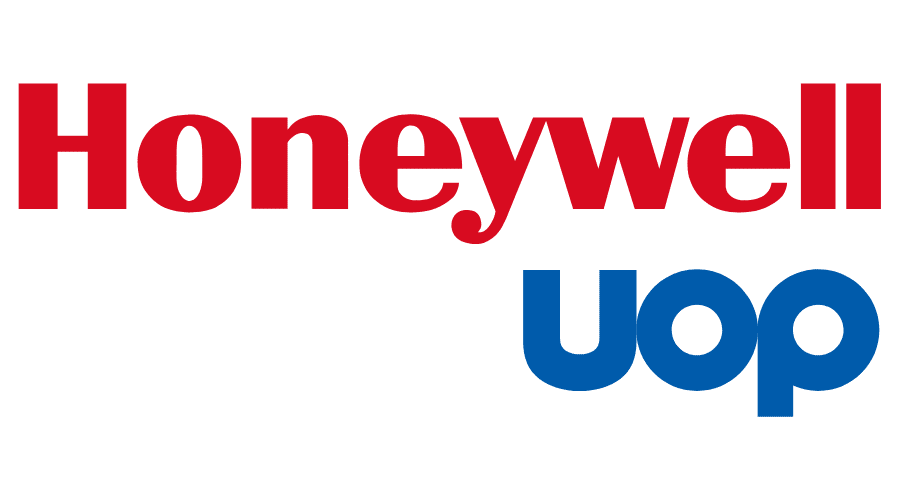
- Name
- UOP Penex
- Owner
-
/ Honeywell UOP
- Brand
- Technology is registered for Trademark Penex™ Process
- Process
- Fuel Processes
- Type
- Isomerization into High-Octane Isomerate
- Available
- Description
-
The Isomerization process in a petroleum refinery is the catalytic process that converts low-octane number straight-chain hydrocarbon molecules (C4, C5, C6) into branched-chain hydrocarbons with the same carbon number and high-octane number. The isomerization reaction rearranges the carbon skeleton of a molecule without adding or removing anything from the original material and transforms the normal paraffins into iso-paraffins. The table shows the difference in RON between normal and iso components.
Objectives of Isomerization Process in Oil Refinery
The isomerization process in oil refining is critical in the current scenario of clean fuels and serves the following purposes ;
- Improves the RON (Research Octane Number) of light naphtha gasoline from 65 to 92, depending upon the Isomerization unit configuration, catalyst type, and requirement of the refiner.
- Removes, benzene, and aromatics form the naphtha and make an ideal blending component for the gasoline pool.
- In the case of isomerization of Butane, it is used to prepare feed for the alkylation unit.
- Helps the oil refinery to manage the gasoline pool by providing high RON naphtha. Low-quality straight-run C5~C6 gasoline is difficult to blend with other gasoline streams, therefore creating a bottleneck for the refinery operation.
In a typical isomerization unit, light naphtha is first hydrotreated and then dried to remove any moisture content. Similarly, from the hydrogen gas stream, H2S is removed in the guard bed reactor and Oxygenates (CO, CO2) are converted to water (H2O) and methane (CH4) in a Methanator reactor. Afterwards, hydrogen gas is dried and mixed with naphtha feed. A small amount of organic chloride is injected into the combined feed stream and then heated to the reaction temperature. After mixing the dry and treated feed and gas streams, the combined feed is preheated by the reactor effluent and then finally heated in a heater up to the required reaction temperature. Process requirement determines whether one or more reactors are to be used.
- Link
System Info
- Updated by
-
Kokel, Nicolas
- Updated
- 12/1/2022 12:25 PM
- Added by
-
Hussain, Nasir
- Added
- 11/25/2022 7:42 PM

No Services yet available.
Go to Solutions to enquire how we can help you or how you can market your own expertise.
Enquire in Solutions how we can help you.