ppPLUS: Technologies and more
Go to Homepage to browse companies and process data
ppPLUS-Solutions providing Services and Support
Register creating your own models
Technology
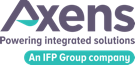
- Name
- Axens R2R
- Owner
-
/ Axens SA
- Brand
- R2R™
- Process
- Cracking
- Type
- Fluid Catalytic Cracking
- Available
- Description
-
Residue Cracking: Two-Stage R2R™
When processing residues containing high levels of metals (Ni, V and Na) and ConC values in excess of 3 wt.%, more sophisticated FCC designs are required.
The Reactor-2-Regenerator (R2R™) design was developed to specifically meet the challenge of heavy resid processing.
The R2R™ process scheme put emphasis on the regeneration system, as the reaction system is nearly identical to the single stage FCC design.
The unique two-stage regeneration system permits safe regeneration of catalyst containing high levels of metals, principally vanadium that would otherwise rapidly deactivate the catalyst.
The first regenerator burns 30-70% of the coke and essentially all of the hydrogen in the coke. Regeneration conditions are mild and vanadium on the catalyst cannot form V2O5 due to the incomplete combustion mode of regeneration. The catalyst is therefore protected from vanadic acid attack. The partial burn, first stage regenerator also provides significant heat rejection in the form of CO. The R2R™ includes the most advanced components in FCC technology, including: impact feed injectors, RS2™ riser termination device, KFBE™ structured stripper packing, SCMSM selective cracking mixer and PetroRiser™ external riser for propylene production. The unique two-stage regeneration system permits safe regeneration of catalyst containing high levels of metals, principally vanadium that would otherwise rapidly deactivate the catalyst.
In the second regenerator, the catalytic activity is restored by completely removing the remaining coke from the catalyst in a dry atmosphere (hydrogen removed in First Regenerator). As such, when V2O5 is formed at elevated temperature, there is little moisture available to form vanadic acid and hence the catalyst structure and activity are preserved. The two-stage regeneration system allows an Axens' unit to operate at significantly higher metals levels on the catalyst, thereby reducing the catalyst make-up requirements and operating cost.
Additional reactor section enhancements include:
- MTC to enhance feed vaporization and control the riser temperature profile for operation in distillate mode.
- Riser Mixor element to limit catalyst back-mixing and enhance yield selectivity.
Heavy Duty Cat Coolers
When additional heat removal is required for either one- or two-stage regenerators, external catalyst coolers can be employed.
Axens offers a proven dense-phase catalyst cooler design. Reliable performance with heat removal duties exceeding 50 MW (>170 million Btu/hr) has been demonstrated. The robust designs feature the highest possible efficiency and flexibility with heat duty control from 0 to 100% by means of positive catalyst flow control.
Literature Reference
Axens, Commercial Bulletin, FCC/R2R™, VGO & Resid Fluid Catalytic Cracking Technology.
- Link
System Info
- Updated by
-
Kokel, Nicolas
- Updated
- 6/28/2024 12:40 PM
- Added by
-
Kokel, Nicolas
- Added
- 11/29/2022 5:57 PM

No Services yet available.
Go to Solutions to enquire how we can help you or how you can market your own expertise.
Enquire in Solutions how we can help you.