ppPLUS: Technologies and more
Go to Homepage to browse companies and process data
ppPLUS-Solutions providing Services and Support
Register creating your own models
Technology
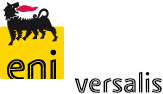
- Name
- Versalis S-SBR
- Owner
-
/ Versalis S.p.A.
- Brand
- Versalis Solution SBR Technology
- Process
- Synthetic Rubber Processes
- Type
- Styrene Butadiene Copolymer Processes
- Available
- Description
-
Introduction to Versalis Solution SBR Technology
Depending on desired product and application, batch and continuous polymerization processes are available in Versalis solution SBR technology.
Main technology highlights are as it follows:
- large production flexibility due to availability of both batch and continuous polymerization technologies, whose selection is driven by the final application of the product;
- cyclopentane, cyclohexane or n-Hexane or blend highly compatible with all different polymer compositions, can be used as solvent depending on local climate conditions;
- high and medium vinyl grades as well as Dry and Oil Extended polymers are allowed;
- production of polymers with linear radial or branched different macrostructures;
- process design advanced features in polymerization and purification sections;
- small quantity of volatile organic compounds (solvent) entering finishing section (low release during extrusion);
- optimized configuration of the stripping section with three stages arrangement to minimize steam consumption without impacting emissions of voc.
Plant Capacities
Versalis S-SBR technology allows to provide with a single line a fairly broad range of economically feasible capacities: up to 65 kt/y per reaction unit, up to 40 Kt/y per finishing line (batch grades), up to 45 kt/y per finishing line (continuous grades).
Main Process Parameters
Process parameters per metric tonne of S-SBR are as it follows:
- Raw Materials (Butadiene, Styrene, Aromatic Oil)
- Electricity - Continuous Process
- Electricity - Batch Process
- Steam (10 barg Medium Pressure + 6 barg Low Pressure)
1,003 kg
0,56 MWh
0.6 MWh
5.5 MTProcess Description
Solution polymerized styrene-butadiene rubber is obtained by anionic copolymerization of styrene and butadiene initiated by lithium alkyls in paraffine or cycloaliphatic solvent; due to the large difference of reactivity ratios for the two monomers, addition of a living chain-end modifier changing the above-mentioned reactivities is required to obtain a well randomized copolymer.
The rubber macrostructure can be efficiently managed/driven by a proper selection of polymerization type (batch, continuous, as respectively depicted in Fig. 1 and Fig. 2), reaction conditions and suitable coupling or branching agents, greatly enhancing the final properties of vulcanized rubber. It is worth to note that the long chain branching, due to radical reactions forming high molecular weight arms, is a competitive advantage of Versalis technology. The elastic properties of the uncured rubber are then greatly modified, allowing an easier incorporation and dispersion of the fillers.
Processing Steps
- The process is first based on the purification of solvent and monomers through distillation and adsorption operations as well as blanketing with dry nitrogen of all chemical mix and feed tanks, in order to ensure the lowest level of poisons detrimental to polymerization reaction.
- Dry solvent (n-hexane or cyclopentane), styrene, initiator, butadiene and other reactants are continuously loaded to the polymerization reactor train or charged batchwise in a specified sequence to the batch polymerization reactors, depending on grades to be produced. Reaction temperature control is enabled by the use of boiling reactor while the using of proper randomizing agent ensures a complete randomness of styrene with the desired level of vinyl unit.
- The polymerization conditions lead to a practically complete depletion of monomers; at the end of polymerization the living chain ends are terminated by addition of substances which modify the polymer structure; so radial or branched or linear rubber can be obtained in order to match the required properties.
Figure 1 - Versalis Batch S-SBR Process Scheme
Figure 2 - Versalis Continuous S-SBR Process Scheme
- After polymerization completion the solution is then pumped to a blend tank operating at slight pressure. Residual traces of unconverted monomers, together with a portion of the solvent, are flash vaporised, condensed and then recycled to the wet solvent tank, while the concentrated polymer solution is blended in the blend tanks.
- The blended solution with the antioxidant agents is fed to the stripping section where the solvent is removed by steam distillation in the presence of a dispersing agent aimed to control the crumb size in the slurry. The vapours obtained from the stripping section are condensed and the solvent, separated from water by a decanter, is sent to the wet solvent tank.
- The crumb slurry is then pumped to the finishing unit, where the crumb is dewatered on a shaker screen, being the water partly recyrculated to the strippers and partly sent to waste water treatment. The dewatered crumbs are dried in two mechanical extruders in series, cooled with air, weighed and baled.
Industrial References
- First production line was built in Grangemouth (UK) in 1995, based on batch process technology and having a capacity of 30 kt/y,
- In 1999, a new reaction section based on continuous polymerization process technology was built.
- A third unit, based on 100 kt/y capacity with continuous and batch polymerization lines, has been licensed in the Far East and is on stream since 2009.
- Two further plants in the Far East are on stream since 2017:
- a batch one with a capacity of 40 kt/y
- a continuous one with a capacity of 60 kt/y).
- Another plant, based on batch technology (60 kt/y) has been licensed in Middle East and is currently under construction.
Literature Reference
Versalis > Technologies and Licensing > Our technologies for production from traditional raw materials > 23rd Feb 2024, S-SBR.

No Services yet available.
Go to Solutions to enquire how we can help you or how you can market your own expertise.
Enquire in Solutions how we can help you.