ppPLUS: Technologies and more
Go to Homepage to browse companies and process data
ppPLUS-Solutions providing Services and Support
Register creating your own models
Technology
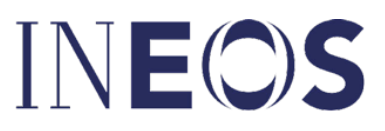
- Name
- INEOS Acrylonitrile
- Owner
-
/ Ineos Technologies (Holdings) Ltd
- Brand
- Acrylonitrile process technology
- Process
- Ammoxidation Reactions
- Type
- Ammoxidation of Propylene into Acrylonitrile (SOHIO Process)
- Available
- Description
-
Overview
The INEOS acrylonitrile process, also known as the SOHIO process, is a catalytic ammoxidation method for producing acrylonitrile (ACN) from propylene, ammonia, and air. INEOS acquired the SOHIO technology after British Petroleum (BP) took over SOHIO in 1987. Today, INEOS is dominant licensor and provider of this technology, claiming that its patented acrylonitrile process technology is used in over 95% of the world's acrylonitrile plants[1],[2]. Key technology aspects are described below.
Reaction Chemistry
The main reaction is:
CH3CH=CH2 + NH3 + 3/2 O2 → CH2=CHCN + 3 H2O
This exothermic reaction (ΔH = -515 kJ/mol) occurs in the presence of a catalyst.
Reactor Design and Operating Conditions
- Uses a fluidized bed reactor system
- Operating conditions: 400-510°C, 5-30 psig
- Catalyst: Bismuth phosphomolybdate or similar mixed metal oxides, typically supported on silica (50% w/w)
- Catalyst consumption: ~0.7-1.0 kg/ton of acrylonitrile
Process Flow
- Reactants (propylene, ammonia, air) are fed into the fluidized bed reactor at a Propylene/Ammonia/Air molar ratio of 1.0/1.1/2.0
- Hot reactor effluent is rapidly quenched in a water scrubber to ~30°C
- Organics are absorbed into an aqueous phase; off-gas is incinerated; unreacted ammonia is neutralized with sulfuric acid
- A series of distillation columns separate and purify the products:
- Recovery column separates crude ACN/HCN overhead
- Extractive distillation purifies ACN using water as an entrainer
- HCN is stripped via fractionation
Heat Recovery
- Steam coils in reactor remove excess heat
- Recovered heat is used to produce high-pressure steam
Process Performance and Byproducts
- Propylene conversion: >98%
- Acrylonitrile selectivity: 80-83%
- Acrylonitrile yield: ~81%
- Acetonitrile: 0.02-0.11 kg per kg acrylonitrile
- Hydrogen cyanide: 0.15-0.20 kg per kg acrylonitrile
References
- North American Catalysis Society, 19th Jan 2012, North American Catalysis Society.
- INEOS > Businesses > Nitriles > About INEOS Nitriles. (accessed 23rd Mar 2025)
- Jack, 2nd Jun 2018, Acrylonitrile Process by INEOS Technologies, Oil & Gas Process Engineering.
- INEOS, Safe Storage and Handling Guide, Created 23rd May 2007, Modified 4th Jan 2016.
- Timothy Robert McDonel et al., US 2016/0256848A1, Filed 4th Mar 2016, Acrylonitrile Manufacture, Assignee: Ineos Europe AG, Status: Abandonned.
- Link
System Info
- Updated by
-
Kokel, Nicolas
- Updated
- 3/23/2025 11:13 AM
- Added by
-
Kokel, Nicolas
- Added
- 3/22/2025 6:59 PM

No Services yet available.
Go to Solutions to enquire how we can help you or how you can market your own expertise.
Enquire in Solutions how we can help you.