ppPLUS: Technologies and more
Go to Homepage to browse companies and process data
ppPLUS-Solutions providing Services and Support
Register creating your own models
Technology
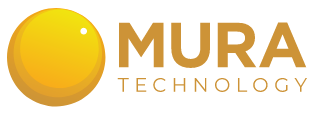
- Name
- MURA HydroPRS
- Owner
-
/ MURA TECHNOLOGY
- Brand
- Technology is registered for Trademark HydroPRS™
- Process
- Molecular Recycling
- Type
- Plastics Pyrolysis
- Available
- Description
-
Hydrothermal Upgrading
Hydrothermal Upgrading (HTU) combines the Process characteristics of Pyrolysis (high heat) and Solvolysis (Dissolution) to heat, melt and then dissolve in Steam the Mixed Plastics Feedstocks under supercritical conditions (>373°C, >220 bar). In this Process environment, Polymers are broken down into Short-Chain Hydrocarbons with the Water acting as a Hydrogen Ion Donor to reduce excess Cracking and Free-Radical Formation. The Steam-Hydrocarbon Mix is then passed through a Column containing a Solid-State Catalyst and depressurised to Flash Distil the Products out across the range of boiling points. The Catalyst is not broken down or consumed in the Reaction, nor does it need Regeneration. Additionally, as it is not a Direct-Heating Combustion Process, HTU does not produce harmful Combustion By-products such as Dioxins or Char as a By-product of Conversion Reactions.[1]
Cat-HTR and HydroPRS Technologies
The HydroPRS Process utilises at its core the Cat-HTR Technology developed by Australia-based Licella Holdings Limited. The 1st-generation Cat-HTR™ Small Pilot Plant was commissioned in 2007 (Fig. 1).[2] The World's first Plant using MURA's HydroPRS™ process, located in Teesside, U.K., is expected to be operational in 2023 with a 20,000 MTA per year Production Line set to supply Dow with a 100% recycled Feedstock.[3]
Figure 1 - 1st-generation Cat-HTR™ Small Pilot Plant in Somersby, Australia
Waste Plastic Feedstock Material Preparation
The HTU Process was modelled on the HydroPRS™ Technology and located at the facility which is currently being constructed at a site in Wilton (Teeside), UK. The Functional Unit for the Study is the Processing of one tonne of Waste Plastic Feedstock. Primary data for the HTU Process was supplied by ReNewELP based on projections from the Facility Design Stage. The supplied Plastic Waste Feedstock is expected to contain non-target Contaminants which need to be removed within a purpose-built Material Preparation Plant (MPP) before the Polymeric Material can be processed within the HTU System. The Feedstock is shredded, and Metal Contaminants are removed at this first stage. A Dry Clean of the shredded Feedstock removes further Solid Contaminants such as Stones, Glass, Wood, Grit etc. These Contaminants are expected to be typically 23 kg of Inert Waste (which will be transported 10 km by Truck to a Landfill), and 8 kg ferrous Metal & 2 kg non-ferrous Metals (which are sold to other Recyclers). Rejects here include PVC, Paper, Dry Cleaner Dust etc. with a total Mass of 72 kg. They are all combustible and are expected to be transported 18 km by truck to an Energy-from-Waste Facility. The remaining 895 kg of Waste Plastic (predominantly LDPE & PP)[1] is undergoing Shredding and Pelletizing.[4]
Simplified Process Description
The pelletized Feedstock is extruded at a Die pressure of about 280 bar and a Barrel temperature of 250°C. Following Extrusion the Polymeric Material is mixed with Aqueous Solvent that has been heated/pressurised prior to contacting the extruded Polymeric Materials. The Reaction Mixture is fed into the Continuous Flow Hydrothermal Reactor by means of a Coupling Arrangement (Fig. 3). The Reaction conditions are shown in Table 1 below.[4]
Figure 3 - Representative Coupling Arrangement between Extruder and Hydrothermal ReactorTable 1 - HydroPRS Processing Conditions according to Ex. 7 in US11339330B2[4]
- mass % Polymeric Feed extruded to Mixing Piece, dry basis
- mass % SWC added at Mixing Piece
- Extruder exit temperature, °C
- SCW temperature at Mixing Piece , °C
- Process Heater entry temperature , after Mixing Piece, °C
- Process Heater exit temperature, °C
- Reactor temperature, °C
- Pressure, bar
- Average Residence Time, minutes
22
78
275
420
390-400
450
430-440
230-260
20-30The Products are Calorific Gas and Light Hydrocarbons, Waxy Oil and Water containing some dissolved Organic Material[4]. The Yields of the five Hydrocarbon Product Streams are as shown in Table 2 below[1]:
Table 2 - Hydrocarbon Product Yields
- Process Gas
- Naphtha
- Distillate Gas Oil
- Heavy Gas Oil
- Heavy Wax Residue
11.4 %
26.0 %
25.3 %
24.3 %
13.0 %Process Inventory
Hydrothermal Upgrading (HTU) is effectively a One-Stage Process (Fig. 2) with several different Inputs as listed below[1]:
- Electricity usage: 16 200 MWh/annum
- Consumption of Potable Water (Fire Water, Safety Showers and general Hygiene): 900 tonnes per annum
- Demineralised Water used in the Boiler: 14,000 tonnes per annum
- Process Water used to enhance the Cooling of the System, particularly during the summer: 8,500 tonnes per annum
- Process Gas used onsite for Steam Generation: 1600 tonnes/annum
- Wastewater Treatment used to remove Contaminants from the Wastewater: 15,768 tonnes per annum
This inventory (Fig. 4) also includes the Separation Stage, whereby the Mixture is depressurised, and Products are separated by Distillation into Five Product Streams.
Figure 4 - Schematic of the Material Preparation and Hydrothermal Upgrading Process
Process Emissions
The overall CO2 Emisisons based on the currently available data, are 478 kg CO2 eq. per tonne of Input Feedstock. The CO2 Emissions of the HTU process are estimated to be 341 kg CO2 eq. mainly reflecting Process Gas Consumption in the High-Pressure Boiler but also Consumption on-site in a Low-Pressure Boiler for ancillary activities. The HTU Process will reuse Gas generated as a Product Stream so the Process does not source Natural Gas from the Grid but the Gas is still being generated from what was originally a Fossil-based Source and the Emissions should be accounted for[1].
Table 3 - Process CO2 equivalent Emissions per Metric Ton Input Feedstock
PROCESS
- Electricity consumption
- Process emissions
- Demineralised water consumption
- Others
- TOTAL
kg CO2 eq. / MT Input Feedstock
201
126
13
1
3411. Ozoemena, M.; Coles, S. Hydrothermal Upgrading of Waste Plastics: An Environmental Impact Study. Preprints 2022, 2022070241. https://doi.org/10.20944/preprints202207.0241.v2.
2. Licella Website Information, accessed on 9 Mar 2023.
3. DOW Corporate Website, 21 Jul 2022, Dow and Mura Technology announce largest commitment of its kind to scale advanced recycling of plastics.
4. US11339330B2, Method and Apparatus for producing Biofuel
5. PlasticsToday Staff, 8 Jan 2020, Chemical recycling of plastics gets a catalytic boost in Australia, China, PLASTICS TODAY
- Link
- Technology #Tags
- #sustainability
System Info
- Updated by
-
Kokel, Nicolas
- Updated
- 6/3/2025 7:45 PM
- Added by
-
Kokel, Nicolas
- Added
- 3/9/2023 6:42 PM