ppPLUS: Technologies and more
Go to Homepage to browse companies and process data
ppPLUS-Solutions providing Services and Support
Register creating your own models
Technology
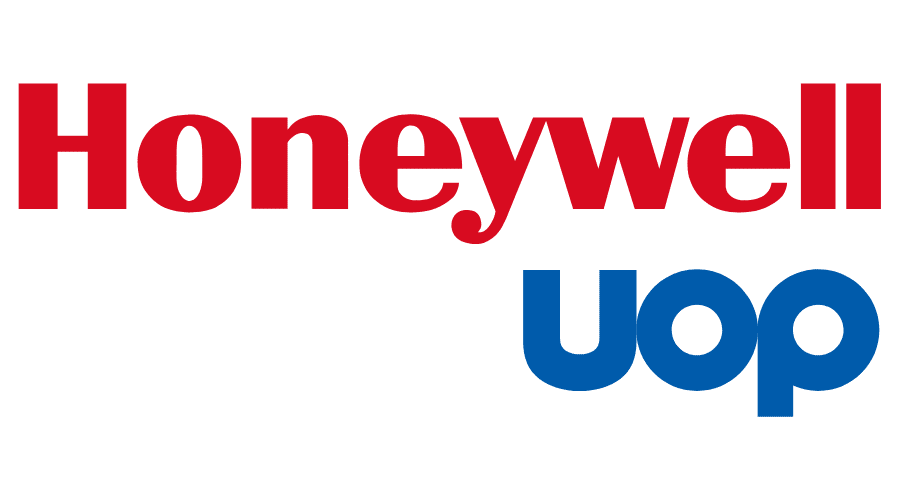
- Name
- UOP CCR Platforming
- Owner
-
/ Honeywell UOP
- Brand
- UOP CCR Platforming™
- Process
- Fuel Processes
- Type
- Catalytic Reforming
- Available
- Description
-
The CCR Platforming™ process is a continuous catalytic reforming technology developed by Honeywell UOP to convert low-octane naphtha into high-octane gasoline blending components and aromatics for petrochemical production, while generating hydrogen as a byproduct. This process enabled lead-free gasoline production through its innovative continuous catalyst regeneration system.
Process Overview (illustration)
- Feed Preparation
Hydrotreated naphtha feed (C6-C11 hydrocarbons) is combined with recycled hydrogen gas and preheated in a combined feed exchanger using reactor effluent heat.
- Reactor Section
- Uses 3-4 vertically stacked radial-flow reactors with platinum-based catalyst
- Endothermic reactions require interheaters between reactors to maintain 480-525°C reaction temperatures
- Key reactions occur through dual-function catalyst (acid and metal sites) — Fig. 1:
- Dehydrogenation of naphthenes to aromatics
- Isomerization of paraffins
- Dehydrocyclization of paraffins to aromatics
- Product Separation
Reactor effluent is cooled and separated in a gas-liquid separator:- Vapor phase: Hydrogen-rich gas (65-90% purity) partially recycled, remainder sent to refinery hydrogen network
- Liquid phase: Sent to stabilizer column to remove light ends, producing high-octane reformate (RON 100-106)
Figure 1 - UOP CCR Platforming Generalized Reaction Scheme.
Continuous Catalyst Regeneration (CCR) System
The defining feature enabling continuous operation:
- Spent catalyst (0.5-1.5% coke) flows by gravity from reactor stack to regenerator
- Regeneration steps:
- Coke combustion (500-550°C)
- Oxychlorination to redisperse platinum
- Drying and reduction
- Regenerated catalyst (0.02% residual coke) returns to top reactor
- Maintains constant activity with <0.1 RON octane drop over 10+ years
Key Advantages
- Operational Efficiency
"98% on-stream factor vs 90-92% for semi-regenerative units" - Yield Optimization
3-5% higher liquid yield and 30-50% more hydrogen vs semi-regenerative systems - Feed Flexibility
Processes paraffinic and cracked naphthas that would rapidly deactivate conventional catalysts - Environmental Impact
Enabled elimination of lead additives from gasoline through high-octane reformate production
Technical Specifications
Parameter Value/Range Operating pressure 3-10 bar(g) Reactor temperature 480-525°C Catalyst circulation 100-600 kg/h Hydrogen production 300-600 Nm³/ton feed Reformate yield 82-86 wt%
Commercial ExperienceFirst commercialized in 1971, over 380 CCR Platforming units have been licensed globally, processing more than 6 million barrels per day. Recent advancements include improved chloride management systems and R-234 catalyst introduced in 2020, achieving 99% of theoretical maximum reforming efficiency.
References
- Edward R. Morgan, Jan 2021, Fifty years of CCR platforming, Honeywell UOP.
- UOP4523-2b, Sep 2016, UOP CCR Platforming Motor Fuel Datasheet, Honeywell UOP.
- Dorr Dikora, 14th May 2013 (last published), CCR Platforming PDF, retrieved via the Web Archive.
- Feed Preparation
- Link
System Info
- Updated by
-
Kokel, Nicolas
- Updated
- 4/25/2025 8:31 AM
- Added by
-
Kokel, Nicolas
- Added
- 11/24/2024 2:14 PM

No Services yet available.
Go to Solutions to enquire how we can help you or how you can market your own expertise.
Enquire in Solutions how we can help you.