ppPLUS: Technologies and more
Go to Homepage to browse companies and process data
ppPLUS-Solutions providing Services and Support
Register creating your own models
Technology
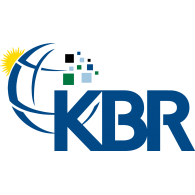
- Name
- KBR VCC
- Owner
-
/ Kellogg, Brown & Root Inc.
- Brand
- Technology is registered for Trademark Veba Combi-Cracking Technology
- Process
- Cracking
- Type
- Resid Hydrocracking
- Available
- Description
-
Overview
The Veba Combi-Cracking Technology (VCC™) is a slurry-phase hydrogenation and hydrocracking technology designed to convert heavy hydrocarbons into lighter, high-quality liquid products. Initially developed as a coal liquefaction process, VCC was commercialized in the 1930s to produce liquid fuels from coal. By the 1950s and 1960s, it evolved into a residue hydrocracking technology under German company Veba Oel, focusing on upgrading heavy oil residues. The Bottrop demonstration plant in Germany, operational from 1981 to 2000, showcased its ability to process diverse feedstocks, including petroleum residues and waste materials. After BP acquired Veba Oel in 2002, the technology was refined for broader applications and scalability. In 2010, BP partnered with KBR for global licensing, leading to the construction of modern VCC units worldwide.
Feedstock
Suitable feedstocks include petroleum residues (e.g., vacuum residues, visbreaker residue), coal, coal tar, FCC slurry oils and pyrolysis oils, deasphalter bottoms, and waste materials (used lubricants, chlorinated solvents, spent catalysts, activated carbon, and mixed plastics).
Step-by-Step Process Description
Feed Preparation
- The heavy feedstock is first slurried with a proprietary finely ground additive.
- This slurry is then mixed with hydrogen gas (both recycled and fresh make-up hydrogen) and heated to the required reactor inlet temperature.
Step Reactor System
- Liquid-Phase Hydrogenation (LPH Reactor):
The slurry mixture enters the liquid-phase hydrogenation reactor operating at high pressure (up to 250 bar) and temperatures typically between 440°C and 485°C. In this reactor, heavy hydrocarbon molecules are cracked into lighter fractions by hydrogenation reactions. Conversion rates exceed 95% in a once-through operation without recycling unconverted residues.
- Hot Separator & Vacuum Flasher
After leaving the LPH reactor, the mixture enters a hot separator vessel where vaporized reaction products (lighter hydrocarbons) are separated from unconverted heavy residue and additive particles. The bottoms from the hot separator (containing unconverted residue and additive) are routed to a vacuum flasher for additional recovery of valuable distillates. -
Gas-Phase Hydrotreatment/Hydrocracking (GPH Reactor)
Vapors from the hot separator and liquids from vacuum flashing are combined and fed into a fixed-bed catalytic hydrotreatment reactor (GPH unit). This step further upgrades products by removing sulfur, nitrogen, and saturating aromatics under slightly lower temperatures than the first reactor but similar high pressures -
Product Fractionation & Separation
After hydrotreatment, the resulting synthetic crude oil (SCO) is cooled, condensed, and separated from recycle gas. The recycle gas is cleaned via lean oil washing before being returned to the LPH reactor for reuse.
Process Capacities and Technology Features
Commercially implemented VCC plants have capacities ranging from 450 thousand tons per annum up to 2.7 million metric tons per annum. Typical operational efficiency includes:
- High once-through conversion rate (>95% residue conversion), eliminating the need for recycling or asphaltene removal.
- Simple flow sheet architecture with traditional refinery equipment and no reactor internals.
- Proprietary additive usage to prevent fouling and enhance conversion efficiency.
- High operational reliability (92% on-stream factor, over 8,000 hours/year uptime).
- Flexible operation from 60% to 110% of design capacity.
- Liquid yields exceeding 100 vol.% due to volume expansion upon cracking.
- Significant aromatics saturation (>75%) under typical operating conditions.
- Liquid yields above 100 vol.% due to hydrogen addition.
- Hydrogen consumption around 360 Nm³ per ton of typical feedstock processed.
- Slurry reactors operate in an up-flow mode without internal structures, simplifying operation and maintenance.
Product Portfolio
The final upgraded products include:
Product Typical Yield (%) Quality Features Applications Naphtha 14-30 Low sulphur (<50 ppm),
low nitrogenPetrochemicals production or
reformer feedDiesel 42-64 Sulphur <10 ppm,
high cetane indexDirect blending into ULSD pool Jet Fuel 17-28 Sulphur <10 ppm,
low freezing point (-46.5°C), high smoke pointAviation fuel Vacuum
Gas Oil9-27 Sulphur <100 ppm,
low metals contentFeedstock for
hydrocrackers/FCC
The product slate can be adjusted according to market demands by changing operating conditions in the second-stage GPH reactor.The small amount of unconverted residue (typically ≤6%) can be:
- Used as fuel in combustion units.
- Further processed via coking or gasification technologies.
- Applied as binder material in coke ovens for blast furnace coke production.
References
- KBR, Jul 2919, VCC™ Veba Combi-Cracking Technology.
- Arseny Favstritsky, 9th Nov 2022, HRCC: raw materials — worse, products — cleaner.
- Link
System Info
- Updated by
-
Kokel, Nicolas
- Updated
- 3/15/2025 6:46 PM
- Added by
-
Kokel, Nicolas
- Added
- 3/15/2025 5:40 PM

No Services yet available.
Go to Solutions to enquire how we can help you or how you can market your own expertise.
Enquire in Solutions how we can help you.