ppPLUS: Technologies and more
Go to Homepage to browse companies and process data
ppPLUS-Solutions providing Services and Support
Register creating your own models
Technology
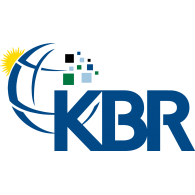
- Name
- KBR ExxonMobil SCORE
- Owner
-
/ Kellogg, Brown & Root Inc.
- Brand
- Technology is registered for Trademark SCORE™
- Process
- Cracking
- Type
- Steam Cracking
- Available
- Description
-
Process Summary
The Proprietary Selective Cracking Optimum REcovery (SCORE) pyrolysis furnace features a single straight radiant-tube design with feed entering the bottom and cracked gas leaving the top of the furnace. This results in low practical reaction time (~0.1 seconds) in the industry, low operating pressures, and high olefins yields. Additional features of the SCORE process are hybrid cracking, online decoking and ultra low-NOx burners. The recovery section is based on a front-end acetylene reactor design pioneered by KBR combined with integration of fractionators with the major compressors[1].
Process Flow Scheme
The pyrolysis furnace (1) cracks the feed hydrocarbon in the presence of dilution steam into large amounts of ethylene, propylene and byproducts. The furnace effluent is cooled by generating steam (2) and quenched further (3–5) to remove heavy gasoline (7), fuel oil and dilution steam. The cooled process gas is compressed (6), caustic-washed (8) and dried (9). The first fractionator is typically a deethanizer for lightgas feeds or a depropanizer for heavier feeds. Both schemes were pioneered by KBR and share common attributes leading to low cost and energy. The example which follows is for a depropanizer-first scheme. The depropanizer (10) is heat pumped by the last stage of the cracked-gas compressor (6). The acetylene in the depropanizer overhead is hydrogenated in an acetylene reactor (11), and the C3 and lighter stream is sent to the demethanizer system (12–14) to separate methane and lighter fraction from the mixed C2/C3 stream. The demethanizer (13) bottoms C2/C3 stream is sent to the deethanizer (15), which is integrated with the heat-pumped C2 splitter (16) and C2 refrigeration compressor (17) in a patented design to save both energy and capital. The C2 splitter is operated at low pressure to produce ethylene product and ethane recycle. The deethanizer bottoms (mixed C3 stream) flows to the C3 splitter (18) where propylene is recovered and propane recycled. The depropanizer bottoms product (C4+ stream) flows to the debutanizer (19) for recovery of the mixed C4 product and aromatic-rich pyrolysis gasoline.
Figure 1 - KBR SCORE Simplified PFD[1].
Plant Configuration
KBR Score plants can be designed with a Deethanizer First (Fig. 2) or Depropanizer First (Fig. 1 & Fig. 3) configuration[2].
Figure 2 - KBR SCORE Deethanizer First Configuration[2].
Figure 3 - KBR SCORE Deethanizer First Configuration[2].
Process Characteristics
Product yiels: Ethylene yields up to to 84% for ethane, 38% for naphtha and 32% for gasoils may be achieved[1] depending depending upon feedstock character (Fig. 4) and cracking severity (Fig. 4)[2].
Energy: overall specific energy per tonne of ethylene ranges from 3,000 kcal/kg to 6,000 kcal/kg, depending on feed type and battery limit conditions[1].
Figure 4 - KBR SCORE Product Yields vs. Feedstock Type[2].
Figure 5 - KBR SCORE Product Yields vs. Cracking Severity[2].
Technology Ownership
KBR's SCORE™ ethylene technology originated from a formal collaboration between KBR and ExxonMobil, combining proprietary innovations from both companies. In 1998, both companies signed a licensing agreement to merge their respective steam-cracking technologies, design expertise, and operational experience. This collaboration integrated ExxonMobil's "Selective Cracking" furnace technology with KBR's "Optimum Recovery" separation processes, forming SCORE™. ExxonMobil's contributied to furnace design for feedstock flexibility and high light-olefin yields, and KBR contributed to recovery-section engineering for energy efficiency and low capital costs, with KBR leading subsequent commercial deployment and advancements[3].
References
- Hyrocarbon Process Engineering, 5th Jun 2018, Ethylene, SUPERFLEX Process by Kellogg Brown & Root LLC.
- Jeff Caton, Feb 2019, KBR Olefins Technologies Providing Key Flexibility with Optimum Design to Ensure Profitability, Ethylene Middle East Technology Conference.
- Robert A. Meyers, 2005 MacGraw-Hill Education, Handbook of Petrochemicals Production Processes, ISBN: 9780071410427, 6.3. KBR SCORE™ ETHYLENE TECHNOLOGY.
- Link
System Info
- Updated by
-
Kokel, Nicolas
- Updated
- 6/25/2025 4:57 PM
- Added by
-
Braun, Uwe
- Added
- 3/7/2021 1:44 PM

No Services yet available.
Go to Solutions to enquire how we can help you or how you can market your own expertise.
Enquire in Solutions how we can help you.