ppPLUS: Technologies and more
Go to Homepage to browse companies and process data
ppPLUS-Solutions providing Services and Support
Register creating your own models
Technology
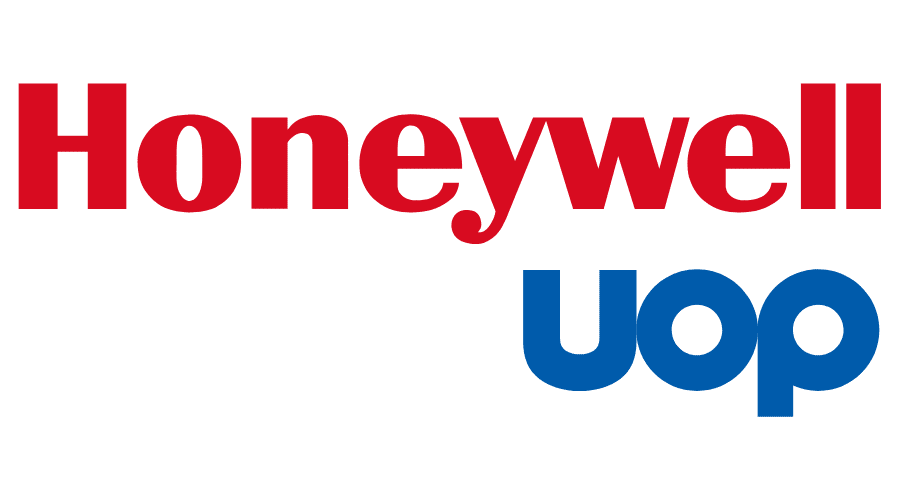
- Name
- UOP ED Sulfolane
- Owner
-
/ Honeywell UOP
- Brand
- Technology is registered for Trademark ED Sulfolane™
- Process
- Separation Processes
- Type
- BTX Separation
- Available
- Description
-
Process Summary
Honeywell UOP’s ED Sulfolane™ process exploits sulfolane’s high polarity to preferentially dissolve aromatics to recover high-purity benzene and toluene from reformate-derived aromatic cuts in a single extractive distillation (ED) column. Non-aromatics remain in the raffinate, enabling >99.8 wt-% recovery of benzene and toluene. The configuration minimizes capital cost, offers low energy intensity, and fits seamlessly into integrated aromatics complexes where feed preparation, downstream fractionation, and auxiliary solvent management are already in place.
Technology Evolution
The sulfolane solvent was commercialized by Shell in 1962 for butadiene extraction; UOP became exclusive licensor in 1965 and secured its first UOP-specific patent in 1971. As operating experience accumulated, UOP migrated from the original liquid-liquid extractor/stripper flowsheet to today’s ED arrangement, removing one large contacting tower while preserving selectivity and capacity advantages.
Chemistry and Solvent Selectivity
Sulfolane (tetrahydrothiophene-1,1-dioxide) is a highly polar, aprotic solvent with strong dipole–π affinity for aromatic rings, yet negligible solubility for saturated hydrocarbons. The solvent’s boiling point is 285 °C; its freezing point is 27.5 °C; and its density at 30 °C is 1.261 g/cm³, enabling stable operation across refinery temperature swings.
Design Basis Snapshot
Parameter Value Notes Plant capacity 1.12 million t/y feed Equivalent to ≈710 KMTA
or 17,000 BPSDFeed aromatic content 67 Liquid Volume % C₆–C₇ reformate
splitter overheadISBL Capital US$29 million
(2010 USGC basis)ED flow scheme only Feed Handling and Complex Integration
The BT cut is withdrawn from the reformate splitter overhead where benzene and toluene have concentrated; its pressure is let down, heat-balanced via a feed/raffinate exchanger, then routed directly to the ED column. Positioning the extraction unit at this point minimizes non-aromatic load, thereby shrinking solvent circulation and column sizing.
Detailed Process Flow
1. Feed Injection Section
The preheated feed and lean sulfolane enter a Rotating Disc Contactor (RDC) tray deck near the top of the ED column when a combined liquid-liquid/extractive scheme is selected. When ED alone suffices, the RDC is omitted and the feed joins the rectifying zone above the solvent entry.
2. Extractive Distillation Zone
Operating at ≈120 °C and 100–400 mm Hg abs., the column contacts rising vapours with descending sulfolane; aromatics dissolve into the liquid down-flow while raffinate hydrocarbons strip overhead as a C₆–C₇ gasoline blendstock.
Column and Internals Specification
Item Detail Justification Extractor type Rotating Disc Contactor
(≤4 m diameter)High stage efficiency
or difficult feedsTray count 35–55 trays total
(combined ED/recovery)Matches target
benzene purityMaterial selection 316L SS with 300-lb flanges
n vacuum shellsLimits oxygen ingress,
mitigates corrosionOperating Conditions
Parameter Typical Range Reference Column top pressure 100–400 mm Hg abs. Vacuum service Solvent/feed ratio 3:1–4:1 wt/wt Balanced for ≥99.9 wt-% benzene Solvent water content 0.3–0.5 wt-% Maximizes selectivity Maximum reboiler T <182 °C Prevents sulfolane breakdown 3. Aromatics Recovery Column
Bottoms from the ED tower flow to a vacuum recovery column where benzene/toluene vapours distil overhead at temperatures below 182 °C, protecting sulfolane from thermal degradation.
4. Clay Treatment Section
Two parallel clay treater drums polish the recovered aromatics, adsorbing trace diolefins and color bodies to satisfy ASTM “Refined Benzene-545” or “Benzene for Cyclohexane Feedstock” quality limits.
5. Raffinate Water-Wash System
Overhead raffinate is scrubbed counter-currently with water to strip residual sulfolane; the solvent-laden water then enters a dedicated water stripper whose vapour is recycled as stripping steam in the recovery column, closing the solvent loop. Raffinate typically contains <5 ppm sulfolane, meeting downstream gasoline pool specifications.
6. Solvent Regeneration
A 3–15 gpm slip-stream of lean solvent enters a small vacuum still operated below 360 °F (182 °C); heavy degradation products accumulate as still bottoms for intermittent disposal, while distilled sulfolane returns to the lean surge drum.
Process Performance and Efficiency
Performance Metrics
Metric Value Comment Benzene recovery ≥99.9 wt-% Commercial average Toluene recovery ≥99.8 wt-% Demonstrated Product purity ≥99 wt-% Meets nitration grade Solvent loss <5 ppm feed Negligible makeup Solvent recycle ≥99 wt-% Closed loop Digitalization and Advanced Control
Modern plants employ model-predictive control to stabilize solvent/feed ratio and column temperature profile while minimizing steam per tonne of feed; on-line densitometers track sulfolane water content to keep selectivity at design targets
Utilities and Energy Demand
Utility Consumption Basis Electricity 5.6 kWh/t feed 1.12 Mt/y plant LP Steam 0.33 t/t feed Same Cooling Water 4.2 m³/t feed Same Net Energy 275–300 kcal/kg extract 99.9 wt-% benzene case Economic Assessment
The 1.12 Mt per year reference design shows an ISBL investment of US$29 million and delivers the lowest specific utility cost among commercial BTX extractions, aided by vacuum operation, small solvent inventory, and one-tower configuration. Compared with the earlier liquid-liquid design, capital is cut by ≈80%, and typical revamp payback is <12 months when replacing aging extractors.
Maintenance, Turnaround, and Corrosion Control
Scheduled clay-bed switchover is the principal routine maintenance activity; clay life exceeds 18 months under typical feeds. Reboiler and exchanger bundles are inspected every four-year turnaround to confirm absence of pitting linked to sulfolane degradation acids; corrosion coupons verify metal loss remains <3 mils per year in 316L sections.
Commercial Footprint and Integration
At least 149 ED or legacy sulfolane units had been licensed by 2006, with additional plants sanctioned in Brunei and Thailand in the 2010s; recent Asian mega-complexes rely solely on the ED configuration for benzene/toluene blocks.
ED Sulfolane™ acts upstream of Parex™ para-xylene recovery, Isomar™ xylene isomerization, CCR Platforming™ reformer feeds, and Tatoray™ disproportionation units, providing feed flexibility while maintaining solvent purity through coordinated chloride management across the complex.
Information Sources
- Sulfolane - Wikipedia
- Sulfolane (C₄H₈O₂S) physical and chemical data - PubChem
- R.J. Uitti et al.; United States patent US 3,590,092: Method for Aromatic Hydrocarbon Recovery; Patent filed on Sep 11, 1968 and granted on Jun 29, 1971; Assigned to Universal Oil Products Co. (UOP)
- Country Engineer | Sep 3, 2022 - Naver Blog - Process License: [UOP] Extractive Distillation Sulfolane Process for Benzene/Toluene Aromatics - Naver Blog
- UOP LLC | 2006 - Sulfolane™ Process commercial bulletin - SCRIBD
- Komex International Ltd. | Aug 6, 2003 - Water Quality Guidelines for Sulfolane - Government of British Columbia.
- Olga Steward & Lisa Minnear, OASIS Environmental | Jun 1, 2010 - Sulfolane Technical Assistance Evaluation Report - Alaska Department of Environmental Conservation
- Aromatics Recovery - Honeywell UOP
- Donald F. Schneider, Stratus Engineering, Inc. | 2003 - Extraction Unit Sulfolane Solvent Regeneration
- Thomas J. Stoodt and Antoine Negiz, UOP LLC | 2004 - Handbook of Petroleum Refining Processes, Chapter 2.2: UOP Sulfolane Process - Handbook of Petroleum Refining Processes - SCRIBD
- Apr 2, 2013 - Honeywell's UOP Technology Selected for Petrochemicals Complex in Brunei - PR Newswire
- Honeywell | May 24, 2018 - Thailand’s IRPC To Build Large Aromatics Complex with Honeywell Technology
- Feb 8, 2021 - Honeywell UOP to provide key technologies, licensing for aromatics complex - Hydrocarbon Processing
- Link
System Info
- Updated by
-
Kokel, Nicolas
- Updated
- 7/23/2025 4:44 PM
- Added by
-
Kokel, Nicolas
- Added
- 11/24/2024 8:49 AM

No Services yet available.
Go to Solutions to enquire how we can help you or how you can market your own expertise.
Enquire in Solutions how we can help you.