ppPLUS: Technologies and more
Go to Homepage to browse companies and process data
ppPLUS-Solutions providing Services and Support
Register creating your own models
Technology
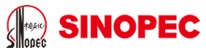
- Name
- SINOPEC CBL Steam Cracking
- Owner
-
/ China Petrochemical Technology Company, Ltd.
- Brand
- CBL Steam Cracking
- Process
- Cracking
- Type
- Steam Cracking
- Available
- Description
-
Introduction
SINOPEC started the development of CBL Cracking Furnace technology in 1984 and the first commercial plant was set up at Liaoyang Petrochemical Co. of PetroChina in 1988. To date, CBL I-VII cracking furnaces have been developed. The single furnace capacity has been increased from 20 KTA to 150 KTA, and the feedstock ranges from ethane to HVGO. CBL technology was selected by many petrochemical companies in/outside China. There are 40 furnaces with single furnace capacity below 100 KTA, and the total capacity is about 2,200 KTA. There are 64 furnaces with single furnace capacity above or equal to 100 KTA, and their total capacity is about 7,690 KTA[1].
Technical Characteristics of CBL Cracking Furnace Technology
CBL technology is a state-of-the-art technology with low investment both for grass root and revamping furnaces. CBL furnace with high feed flexibility could be applicable to different feedstock such as ethane, light hydrocarbons, NGL, naphtha, light gasoline oil and Hydrotreated VGO, especially for heavy feedstock; CBL technology has special advantages: long run length and high ethylene/propylene yields. SINOPEC swirling element of radiant tube (SERT) could be installed to the radiant coil as anticoking elements to extend the run length to more than 80 days. The furnace could be double firebox with shared convection section, and separate firebox decoking as well as decoking effluent back to firebox can be adopted in the furnace[1].
The characteristics of CBL technology are as it follows[1]:
- Liquid feed
- Two pass high selective coil configurations (2-1(CBL-Ⅲ), (4-1(CBL-Ⅳ), modified 2-1 (CBL-V), modified 1-1 (CBL-VI), etc.) can be selected for different cases. The first pass has small diameter with relatively large specific surface area, resulting in a quick temperature increase; the second pass has relatively large diameter, resulting in a lower pressure drop and helping lower the hydrocarbon partial pressure. Appropriate coils are chosen based on different feeds and capacity requirements. The coil configuration combining with higher coil outlet temperature, shorter residence time and lower hydrocarbon partial pressure leads to the advantages of high cracking selectivity, long run length.
- TLE: 1 or 2-stage TLE can be selected based on different cases. Linear quench cooler is preferred for shorter resident time.
- Dilution steam injection: 1 stage (for light feed) / 2 stages (for heavy feed). By using such technique, the coke formation of heavy oil in convection section coils can be avoided.
- Heat supply: combination of hearth and sidewall burners or hearth burner only. The heat distribution along the radiant coil can be optimized to avoid overheat.
- High thermal efficiency: up to 94-96%.
- Variable Frequency Speed Control driving motor can be adopted for Induced Draft Fan.
- Gas feed
For gas feed, four pass coil configuration is adopted. The TLE could be 2 or 3 stages. For the ethane-cracking furnace, the run length could be longer than 80 days.
Swirling Element of Radiant Tube (SERT)
Feedstock through the tube in the furnace is heated and converted into desired products. In the industrial operation, heat resistance will build up in the tube due to the flow boundary layer and the formation of coke on the inside wall of the tube, thus resulting in over-temperature and shortened run length. The tube with twisted-tape technology developed by SINOPEC can intensify the heat exchange by reducing the heat resistance in the flow boundary layer and reduce coke deposition inside the tube. The innovative tube is a precision cast tube integrated with inside twisted-tape, which is inserted into the reaction tube of the radiation section of cracking furnace. Passing through the twisted-tape, the flow in the reaction tube is forced to change from a plug flow to a swirl flow, which greatly increases the flow rate along the tube perimeter and forms a strong scouring force towards the tube wall. Thus, the thickness of the boundary layer decreases, the heat exchange coefficient increases and the temperature at the tube wall decreases, consequently leading to the decrease of coke formation at the wall and further improving the heat exchange coefficient, and resulting in the intensified heat exchange and a longer run length[2].
The characteristics of SERT are as it follows[2]:
- The SERT is inserted only in a small part of the radiation section of the cracking furnace, so compared with the conventional methods that use heat transfer intensified tube in the whole or half of the tube length, the increase of pressure-drop is significant reduced, and the manufacturing cost is lower.
- Under the same operating conditions, with insertion of the tube with twisted-tape, the temperature at the tube wall can be reduced by at least 20 ºC and the operation cycle of cracking furnace is extended by at least 40%.
- Under the same operating conditions with the same cycles, the throughput of cracking furnace can be increased by about 7%.
Ethylene Recovery Technology (LECT)
Ethylene recovery technology is used for olefin recovering from cracked gas and to produce polymer-grade ethylene, propylene and side products including hydrogen, mixed C4s, gasoline, PGO and PFO[3].
The characteristics of LECT are as it follows[3]:
- The gasoline fractionator uses circulating pan oil to remove heat and to make a better temperature distribution in the tower. Pan oil is meanwhile used as heat source for reboilers of HP/LP depropanizers.
- PFO stripper is used to control the viscosity of the quench oil, resulting in the increase of bottom temperature of gasoline fractionator.
- The 5-stages cracked gas compressor with low compression ratio can reduce the fouling caused by cracked gas inside the compressor.
- The HP/LP-depropanizer system decreases fouling in the reboilers. The C3's overhead of LP depropanizer are sent back to HP depropanizer. All acetylene and large amount of MAPD (Methylacetylene and Propadiene) are removed in C2 hydrogenation system so that the load of C3 hydrogenation system is reduced.
- The catalysts for C2/C3 hydrogenation are independently developed by SINOPEC. No hydrogen is needed either from the cold recovery system or OSBL during the commissioning stage.
- C3 tower washing, C2 washing tower, cold box, pre-demethanizer and demethanizer are involved in the cold area so that the streams will be more reasonably distributed. By using this new process, cold duty will be reduced whereas the ethylene recovery rate will be increased.
- Proprietary Condensating-Fractionate Tower (CFT) is used. It has both heat and mass transfer function, and can separate the materials as well as recycle cold duty.
- Ethylene fractionator and ethylene refrigerant compressor consist of an open heat-pump system. The ethylene fractionator operates at low pressure so that reflux ratio is also low. The heat-pump system reduces the total power of the refrigerant compressor. Equipment cost is reduced by integrating ethylene fractionator heat-pump compressor and ethylene refrigerant compressor into one compressor.
Tail-end Selective HT for Removal of Acetylene in C2 Fraction
The tail-end selective hydrogenation process is applicable to tail-end process ethylene unit for removal of acetylene in C2 fraction. The catalyst used in the process is very important to ethylene cracking units as its performance directly affects profitability of the units. BC-H-20A/B catalyst is a new generation tail-end selective hydrogenation catalyst developed by SINOPEC. It is a multi-metal composite catalyst with high selectivity and high ethylene yield under a wide range of operating conditions. There is no need for the process to introduce CO to adjust selectivity. Compared with the previously developed catalysts of the same kind, BC-H-20A/B catalyst reduces the amount of green oil byproduct and makes the oil lighter. Hence, the green oil is not likely to stick to the catalyst surface but form coke, resulting in longer catalyst regeneration cycle and longer catalyst service life[4].
References
- SINOPEC China Petrochemical Technology Co., Ltd., CBL Furnace Technology. (accessed on 13th Oct 2021).
- SINOPEC China Petrochemical Technology Co., Ltd., Swirling Element of Radiant Tube (SERT). (accessed on 13th Oct 2021).
- SINOPEC China Petrochemical Technology Co., Ltd., Ethylene Recovery Technology (LECT). (accessed on 13th Oct 2021).
- SINOPEC China Petrochemical Technology Co., Ltd., Tail-end Selective HT for Removal of Acetylene in C2 Fraction. (accessed on 13th Oct 2021).
- Liquid feed
- Link
System Info
- Updated by
-
Kokel, Nicolas
- Updated
- 10/15/2024 6:19 AM
- Added by
-
Kokel, Nicolas
- Added
- 10/13/2024 4:31 AM

No Services yet available.
Go to Solutions to enquire how we can help you or how you can market your own expertise.
Enquire in Solutions how we can help you.