ppPLUS: Technologies and more
Go to Homepage to browse companies and process data
ppPLUS-Solutions providing Services and Support
Register creating your own models
Technology
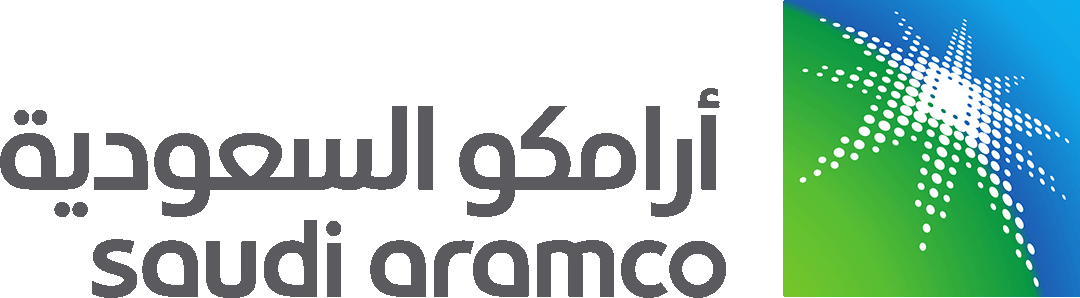
- Name
- TC2C
- Owner
-
/ Saudi Aramco Technologies Company
- Brand
- Thermal Crude to Chemicals (TC2C™)
- Process
- Crude Oil Processing
- Type
- Crude-to-Chemicals
- Available
- Description
-
Technology Summary
Saudi Aramco Technologies Company (SATC), Chevron Lummus Global (CLG) and Lummus Technology LLC jointly developed Thermal Crude to Chemicals (TC2C™), which is a process that integrates whole crude separation, hydrocracking, hydroprocessing and steam cracking to maximize olefin/aromatic yields as per attached Process Flow Diagram.
Feedstock Characteristics
The process is claimed to be crude-agnostic, capable of processing the following crudes:
- Extra Light Crude, e.g. Arab Extra Light: API ~36°, sulfur ~0.047–0.9 wt%
- Ligh Crude, e.g. Arab Light: API ~33°, sulfur ~1.8–2.5 wt%, metals 50–80 ppm
- Medium Crudes
- Condensates
- Low Value Refinery and Petchem Streams
However, Arab Light crude oil is optimal due to balanced fraction as per the Table 1 below:
Table 1 - Feedstock characteristics and preferred crude oil type
Parameter Desalted crude,
condensates,
bitumen oilsArab
LightAPI Gravity 4°-60° ~33° Sulfur 0.009-6 wt% 1.8-2.8 wt% Nitrogen- 0.02-0.95wt% 0~.1 wt% Metals (Ni, V) <1-1000 ppm ~50-80 ppm Boiling Range Up to 700°C 5% BP: 36-54°C
95% BP: 735°CProcess Description
Whole Crude Separation
Desalted crude oil is split into three fractions—light fraction, medium fraction, and heavy residue—by means of proprietary equipment, including an Integrated Separation Device and a Hot Hydrogen Stripper—as described in Table 2 for Arab Light crude oil.
The process involves the following simplified sequence:
Start with crude oil → Heat it up → Spin in cyclone to split into light gases and heavier liquids → Reheat the liquids → Strip with hydrogen to get naphtha/LPG and heavy bottoms.
Table 2 - Arab Light crude separation via TC2C advanced separation devices.
Fraction Boiling
RangeYield Key
PropertiesLight
Fraction<160°C 25% BMCI <5, H₂ >14 wt%, sulfur <1000 ppm,
metals <1 ppm. Direct cracker feed.Medium
Fraction160-490°C 45% BMCI 20–30, sulfur 0.5–2 wt%, metals
<50 ppm. Sent to fixed-bed hydroprocessing.Heavy
Residue>490°C 30% BMCI >50, metals 50–80 ppm, CCR >15%.
ent to hydrocracking.
Integrated Separation DeviceThe Integrated Separation Device (IDS) performs centrifugal/cyclonic vapor-liquid separation. A cyclone works by spinning a mixture of vapor and liquid at high speed inside a cone-shaped device. The spinning force pushes heavier liquids to the walls, where they slide down and exit the bottom, while lighter vapors move to the center and rise out the top, quickly separating the two phases. In case of whole crude, the oil is fed into a heater and warmed up to a high temperature, around 300-400°C. This turns the crude into a hot mix of vapor and liquid, called the pre-heated hydrocarbon feedstock. Heating vaporizes the lighter parts of the crude (like gases and light liquids) while keeping heavier parts as liquid, preparing the crude for separation.
Hot H2 Stripper
The Hot H2 stripper takes the heavier liquid from the cyclonic separator and uses hydrogen to enhance separation efficiency. The stripping column is designed to separate and upgrade the preheated hydrocarbon stream using hot hydrogen gas instead of steam, injected at the bottom of the column as the stripping medium, which improves separation while also facilitating some degree of hydrotreating or saturation by reacting with olefins and sulfur compounds in the feed. The overhead stream becomes rich in light hydrocarbons (e.g., LPG, naphtha) and H2S, while the bottom stream contains heavier, stabilized components.
Hydrogen Recovery via Amine Treatment
The vapor exiting the stripper contains excess hydrogen, H2S (from desulfurization), and light hydrocarbons. This gas is cooled and sent to an amine treatment unit:
- Absorption: in the Amine process, the gas contacts an amine solution (e.g., monoethanolamine or diethanolamine) in an absorber column.
H2S is absorbed (H2S + R-NH2 → R-NH3+HS-), while hydrogen and light hydrocarbons pass through as a purified stream. - Regeneration: The H2S-rich amine is heated in a regenerator, releasing H2S (sent to a sulfur recovery unit, e.g., Claus process) and recycling the lean amine.
- Hydrogen Recycle: The purified hydrogen is recompressed and reheated, then returned to the Hot H2 Stripper, minimizing hydrogen loss and operational costs.
Multi-Stage Fixed-Bed Hydroprocessing (Middle Oil)
The multi-stage fixed-bed catalytic reactor is converting the middle oil, the ebullated-bed hydrocracking effluent and the steam cracker C9+ pygas into naphtha-range hydrocarbons, used as a cracker feedstock.
Ebullated Bed Liquid-Circulation Hydrocracking (Heavy Oil)
The ebullated bed hydrocracking process employs a liquid-circulating catalytic reactor (e.g. LC-Fining) with continuous catalyst replacement to convert the heavy oil + recycled pyrolysis oil from the steam cracker into middle oil through hydrocracking under high hydrogen pressure for downstream hydroprocessing in the Middle Oil Fixed-Bed process.
Fixed-Bed Hydrotreating (Unconverted Oil)
The fixed-bed hydroprocessing process involving demetallization in guard beds and desulfurization reactors removes sulfur from the unconverted oil (UCO) and stabilizes it into Very Low Sulfur Fuel Oil (VLSFO).
Cracker Off-Gas Methanation
A fixed-bed catalytic reactor purifies the hydrogen-rich off-gas from steam cracker (containing CO, CO2) via methanation (CO + 3H2 → CH4 + H2O).
The high purity hydrogen thus obtained is reused in the other processing units, minimizing external hydrogen demand.Steam Cracking
The steam cracker process (e.g. Lummus SRT) employs pyrolysis furnaces to crack the light fraction (~30%), hydroprocessed medium oil (~43%) and the hydrocracked effluent (~27%) based on total cracker feedstock quantity into chemical products. Off-gas is processed in the methanation unit, pyrolysis oil is recirculated to the hydrocracking unit, and the C9+ pygas is sent back to the hydroprocessing unit. Methane recovered from the fuel gas is employed to fuel the complex.
Key Integration
All reactors described in the previous section operate within a shared high-pressure gas loop, reducing equipment count and hydrogen costs. The ebullated-bed and fixed-bed systems align runtimes (3-5 years) with steam cracker decoking cycles, ensuring continuous operation. Overall, the TC2C process is claimed to achieve 70+wt% chemicals yield with 30-40% lower CAPEX/OPEX versus conventional routes.
Mass Balance
Based on 70% conversion rate into chemical products (olefins and aromatics), the following yields from Arab Light crude oil, before steam cracking, are estimated:
- 12wt% ± 5wt% LPG (C3/C4), the majority (~70%) of which originates from the light fraction separation, with smaller contributions from hydroprocessing and hydrocracking.
- 58wt% ± 5wt% naphtha-range hydrocarbons.
- 7.5wt% ± 2.5wt% hydrotreated fuel oil.
- 15wt% fuel gas.
- 7.5wt% process losses.
References
- a. Ujjal Mukherjee et al., US 11365361 B2, Priority Date: 16th Mar 2020, Configuration for olefins production, Assigned to: Saudi Aramco Technologies Co & Chevron Lummus Global LLC & Lummus Technology LLC, Status: Active.
b. Essam Abdullah Al Sayed et. al, US 2022/0056354 A1, Priority data: 5th Nov 2021, Configuration for olefins production, Assigned to: Saudi Aramco Technologies Co & Chevron Lummus Global LLC & Lummus Technology LLC, Status: Pending. - Process Technology Datasheet, 18th Aug 2021, Thermal Crude to Chemicals (TC2C™), Lummus Technology, LLC.
- A.I. assisted assessment of references 1. and 2. above (Grok Deep Search & Perplexity Auto Search), 11th Mar 2025.
- Link
System Info
- Updated by
-
Kokel, Nicolas
- Updated
- 6/20/2025 2:46 PM
- Added by
-
Kokel, Nicolas
- Added
- 3/11/2025 2:57 PM

No Services yet available.
Go to Solutions to enquire how we can help you or how you can market your own expertise.
Enquire in Solutions how we can help you.