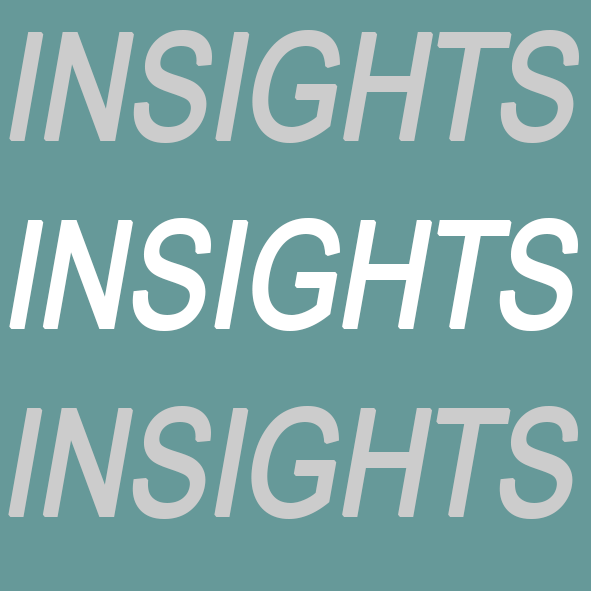
Article
Know Your Renewable Content
|
Renewable Content in Chemicals and Polymers
In recent years, pressures have increased on the chemical industry, especially in Europe, to accelerate the transition to a so-called circular economy, whereas the equivalent to decarbonisation in the energy sector is a transition to carbon from renewable sources in the chemical and plastics industries, aiming at reducing the carbon footprint of its activities.
Renewable carbon in chemical substances possibly originates from only three different sources [1]:
-
Biosphere: Renewable carbon gained from all types of biomass.
-
Technosphere and atmosphere: Renewable carbon from direct carbon dioxide utilization.
-
Technosphere: Renewable carbon from recycling of already existing plastics and other organic chemistry product.
Fig. 1 - Renewable Carbon and Renewable Energy

In the present study we elaborate on renewable carbon originating from the biosphere, that falls under different subcategories [1]:
-
Food crops
-
Non-food crops
-
Side streams, by-products and biogenic waste
-
Includes measurable bio-based carbon content as well as “biomass balance and free allocation” approach.
Fig. 2 - Biogas Production Plant
Substances with a renewable carbon content are also defined as bio-based or bio-sourced chemicals or have 'bio' as a prefix in their name, such as bioethanol made through fermentation of e.g., corn stalks. The renewable carbon content is determined as the ratio between the number of carbon atoms of renewable origin to the total number of carbon atoms in a molecule, which is 100% for bioethanol, but this is not a general case.
For example, a product like Perstorp's 2-Ethylhexanol Pro 25 [2] has 25% of renewable carbon content originating from biomass fermentation into biogas [3] that replaces natural gas using the Mass Balance approach (more on this later) in the subsequent Steam Methane Reforming (SMR) step that produces syngas. The syngas in its turn is used for propylene hydroformylation. The resulting intermediate n-butyraldehyde and the final 2-Ethylhexanol product formed in a multi-stage process both comprise a renewable carbon content (identified in green color in Fig. 3) of 1:4 or 25% by weight.
Fig. 3 - Renewable Carbon Content

This is obviously a desired improvement from a sustainability perspective although the ultimate objective remains to produce molecules that are fully derived from renewable carbon sources, i.e. with a 100% renewable carbon content. In the above example, this could be achieved by combining biogas and renewable - or bio-based - propylene (represented in red colour as a 3-carbon atom fragment).
Bionaphtha for 100% Renewable Carbon Content?
The main avenue being explored towards bio-based light olefins such as ethylene or propylene employs bionaphtha as a steam cracker liquid feedstock in replacement for petroleum naphtha to produce the various chemical building blocks that the steam cracking process makes.
Fig. 4 - Naphtha Cracking (Credit: arab-oil-naturalgas.com)
Naphtha is a light distillate fraction obtained through atmospheric distillation of crude oil. In the steam cracking process the large hydrocarbon molecules in the naphtha liquid are cracked into smaller hydrocarbons and reformed into different molecules, whereby ethylene and propylene are the two main chemical products obtained (Fig.
Technically, bionaphtha is both a second-generation hydrotreated vegetable oil (HVO) product from renewable waste and other biomass products, and a by-product of renewable diesel manufactured through catalytic hydrodeoxygenation processes (Fig. 5) such as the ENI/UOP Ecofining process or the UPM Tall Oil hydrotreatment process to name just these two when in actuality more than half a dozen processes have reached commercial stage.
Fig 5 - Schematic representation of a two-step process for obtaining green naphtha, jet fuel, and renewable diesel coupling hydrodeoxygenation and selective hydrocracking [4]

Such hydrotreatment processes are producing various hydroprocessed esters and fatty acids (HEFA) fuel products such as renewable diesel (C14- C20), sustainable aviation fuel (SAF; C11-C13) and bionaphtha (C5-C10) that can replace their respective petroleum-based analogs - naphtha, kerosene and gasoil - since they are identical in both their compositions and properties with the fossil-based hydrocarbon fuels they displace.
|
Fig. 6 - Hydrocracking of gas oil into gasoline and diesel
on a bifunctional catalyst [4]

However, most of the existing HEFA production plants are geared towards making renewable diesel as a main product since the production of lighter fuels such as SAF and gasoline (a form of naphtha) requires both higher severity conditions (higher temperature and strong acid catalysts) in the hydrodeoxygenation step and a second hydrocracking / isomerization step resulting in higher investment and process costs, and the process also makes a higher proportion of lower value light gases (fuel gas) [4] that is further curtailing the process economics.
We have modeled the mass balance of the UPM Lappeenranta Biorefinery (Fig. 7) that produces 100,000 metric tons of renewable diesel from crude tall oil according to the 2016 version of the Biofuel Fact Sheet - UPM Biofuels - commercial plant in Lappeenranta, Finland, formerly available on the ETIP Bioenergy Website (but now replaced with a newer version that provides less conclusive capacity details).
Fig. 7 - UPM Tall Oil Hydrotreatment Process (©UPM 2022)

For this Mass Balancing exercise we have considered various process characteristics and information details such as by-products, yields, and selectivities. For example, the crude tall oil feedstock needs to undergo evaporation to remove both the tall oil heads and tall oil pitch as described in the Example 2 of US patent US 10,240,095 B2 [5]:
"The purification removes 4 % of the light fraction and 6 % of the heavy pitch fraction providing 90 % of the crude tall oil as purified CTO."
Then we need to account for the process selectivity (Fig. 8), whereas the purified tall oil is undergoing hydrotreatment according to Example 2 of US patent US 10,023,810 B2, that is likely describing the selectivity of the Lappeenranta biorefinery, whereby it occurs that crude tall oil hydroprocessing makes 71% Diesel and 7% Gasoline (Naphtha) by weight, meaning that the total yield of both diesel and gasoline is 78% by weight, but as well that the naphtha fraction makes about 10% by weight of the diesel cut [6].
This raises the question about the nature of the residual 22% by weight of reaction products. We can estimate that reaction water makes 2% by weight of the purified tall oil feedstock [7]. Then according to sections 15 and 20 of US 10,023,810 B2 [6]:
Fig. 8 - Table 2 - Example 2 - US 10,023,810 B2 [6]
"The stream comprising light gaseous components is directed for purification to a separator capable of removing H2S and CO2 from the gaseous stream which forms a recycle stream comprising H2 and light hydrocarbons including methane. Examples of such separators are amine scrubbers (amine solution absorbers) and separation units utilizing membrane technology, suitably an amine scrubber is used. The obtained recycle stream may be directed to the hydroprocessing reactor system."
Since the amounts of neither the recycle stream nor of the light gases are stated in the patent, we make the assumption that 13% by weight of heavier bottoms are sent back to the hydroprocessing reactor system and the balance is therefore made of about 7% by weight of fuel gas that is probably used as a fuel to power a thermal unit.
The outcome is the mass balance table (Fig. 9) or chart view for the Lappeenranta refinery, with an estimated bionaphtha output of about 10,000 metric tons annually.
Fig. 9 - Mass Balance of the UPM Biofuels Lappeenranta Biorefinery

Argus confirms our own estimate by stating that "when producing HVO, the yield of bionaphtha can be up to 10pc (though often it’s lower) while this share grows when producing SAF" [8]. Based upon 2019 renewable diesel capacities in Europe that are estimated at just above 3 million tons (Fig. 10) per year, the available bionaphtha volume can be calculated to be around 200,000 metric tons annually. Another source confirms that by 2021, about 150,000 tons of bio-based naphtha are already used annually in Europe [9].
Fig. 10 - Leading HVO diesel producers in the European Union (EU-28) in 2019, by installed capacity in 1,000 metric tons (Source: statista)
The available European bionaphtha is essentially diverted for the use as a fuel blending component in virtue of the Renewable Energy Directive (RED II), mandating renewable energy to make up 32% of the consumption mix by 2030, and a minimum of 14% renewable energy in road and rail transport among E.U. members by 2030. Second-generation biofuels such as bionaphtha, when produced from waste products such as forestry and agriculture waste products, used cooking oils, animal fat waste, or food industry residues, are counted twice as much towards the mandate, which super-incentivizes their use as renewable fuels.
This is clearly the case with UPM's Bioverno Bionaphtha that is obtained from crude tall oil, a waste product of the paper industry (Fig. 11) separated from black liquor in the Kraft sulfate pulping of mainly coniferous trees [10].
Fig. 11 - The tall oil value chain
On the contrary, fewer legal constrains are weighing on the chemical industry to substitute fossil-based feedstock for bio-sourced products beyond the Single-Use Plastics Directive and the Circular economy action plan. Legislative incentives channeling the use of bionaphtha as a renewable fuel, the already very narrow bionaphtha market, and price multiples to be paid for bionaphtha above the price of petroleum naphtha, combine to discourage any attempts by chemical companies to use bionaphtha as a chemicals feedstock in refining operations.
Any ambitious and courageous undertaking to proceed in this way would be further constrained by the naphtha cracking process yielding limited quantities of valuable building blocks, typically in the 26 to 28% range by weight of ethylene, and in the 17 to 20% range by weight for propylene (Fig. 12) [11]. Using bionaphtha as a sustainable feedstock in a steam cracker would see about half of the renewable carbon atoms to be diverted into useless molecules with only lower fuel value, which does not make worth it bearing the cost.
Fig. 12 - Simulation results and comparison with typical yields
for naphtha cracking [11]

Let's assume a high case where all the European produced bionaphtha (about 200,000 metric tons) is available for refining operations, in which case the total amount of bio-based ethylene at 28% yield would be about 60,000 metric tons (when in good faith it is probably a fraction of this quantity, something like 10,000 metric tons of bio-ethylene since most of the bionaphtha is thought to be committed for fuel blending).
A typical European steam cracker site has an ethylene output in the range from 400,000 to 800,000 metric tons of ethylene (Fig. 13), meaning that in our high case hypothesis the amount of bio-based ethylene that such a single typical cracker could produce in Europe would be about 10% of its ethylene output (60,000 / 600,000) while leaving no single ton of bionaphtha available for any other European cracker.
Fig. 13 - Ethylene capacities in metric tons (left scale) of European steam crackers (source: petrochemistry.eu)

Against the claim that "for the first time in industrial history, the chemical industry can be decoupled from oil and gas" [9], the harsh reality is that renewable carbon content in chemical products and decarbonisation of the chemical industry remains therefore an elusive and distant aspiration.
Claims of Renewable Content and Circularity
The stated constrains and barriers do not, however, discourage chemical companies from sustainability and circularity claims to decarbonise the sector towards a net-zero carbon future, buttressed by the many new Standards and certification schemes, themselves piggy-backing on regulatory requirements, carbon credit schemes, and environmental subsidies.
The Redefining Energy podcast reports that "ESG investing seems to be victim of its own success with inflated claims not met by facts. With more than 600 ratings and 4,500 metrics, ESG has become a maze where investors are drowned in an “alphabet soup” of standards while some financial institutions seem to be more focused on fees than purpose" [12].
In particular, due to the limited amount of available renewable feedstock for refining operations, the chemical industry is rapidly moving towards the adoption of the so-called Mass Balance Approach as a tool to quantify the feeding of renewable mass flows to existing fossil systems and processes, while keeping track of their quantities and allocating them to specific products. Materials are either physically segregated in production processes throughout the supply chain (“physical segregation”) or mixed in production but separated in bookkeeping (“mass balance approach”). (Fig. 14).
Fig. 14 - The Mass Balance Approach for Allocation of Renewable Feedstock
used in Chemical Operations [13]
A producer could buy biogas on the paper market and receive corresponding quotas from the natural gas grid, or it could blend some amounts of bionaphtha with fossil-based feedstock. In both cases the quantity of renewable feedstock is certified by a third party such as a certification body. This results in so-called bio-attributed chemicals and plastics, which commercial volume is proportional to the renewable feedstock share fed into the process.
Corresponding examples are Vynova's bio-attributed PVC, INOVYN's bio-attributed PVC biovyn, INEOS STYROLUTION's bio-attributed styrenics, Trinseo's bio-attributed Polystyrene, ABS, and SAN, INEOS's Bio-attributed Olefins and Polyolefins and Bio-attributed Ethylene Oxide, Perstorp's renewable oxo products [3], DSM's bio-based Dyneema fibers (UHMWPE), and many more.
In particular, producers are claiming access to the same source of renewable feedstock, such as is the case of UPM Biofuels' Bioverno Bionaphtha, as a replacement for fossil raw materials [14]:
-
"INEOS will use UPM BioVerno, a sustainable raw material from a renewable residue of wood pulp processing, to produce bio-attributed polyolefins ../.. Applications also include BIOVYN™️, the world’s first commercially available bio-attributed PVC, produced by INOVYN an INEOS Business" [15]. "The new PVC uses residue from wood pulp manufacturing and is being made at an Ineos Olefins & Polymers plant in Cologne, Germany. The raw material is called UPM BioVerno and has also been used to make bio-attributed polyolefins" [16]
-
"Elopak, Dow and UPM Biofuels joined forces to make a 100% wood-based carton" [14]. "The naphtha, produced from wood and trade named BioVerno by UPM, ultimately is used to produce biobased polyethylene for use in packaging applications. Dow is planning to boost usage of the renewable feedstock after a successful year-long trial" [17]
-
"Royal DSM, SABIC and UPM Biofuels, a leading producer of sustainable raw materials, have announced a partnership that will help to reduce the environmental footprint of Dyneema fibre. ../.. UPM Biofuels produces bio-based feedstock UPM BioVerno from the residue of the pulping process. This is then processed by SABIC to make renewable ethylene under its Trucircle umbrella of solutions" [18]
Fig. 15 - Wood-based cartons made with Bioverno Bionaphtha
What it means is that three world scale naphtha crackers with a total output of roughly 2 million metric tons of ethylene and consuming about 7.5 million metric tons of naphtha are chasing the same 10,000 metric tons of Bioverno bionaphtha also competing with uses of the same 10,000 metric tons for renewable gasoline. Assuming that half the amount of Bioverno goes to fuels and the other half is used as a chemical feedstock, then naphtha substitution rate for the three crackers of Dow, Sabic and Ineos combined would be less than 0.07% and the actual bio-ethylene output would be 5,000 x 27% / 3 or about 450 metric tons per cracker, really a drop of water in a full bathtub.
But still the operators are getting fully certified for their circular activities such as Inovyn receiving a compliance certificate from the Roundtable for Sustainable Biomaterials for the production of polyvinyl chloride, and mother company Ineos an ISCC Plus certificate for the use of bio-circular naphtha at its Köln site in Germany. The certificate evaluation report from the Roundtable for Sustainable Biomaterials of Ineos AG Europe on the use of bionaphtha mentions coordinates corresponding to the larger naphtha cracker at the Doormagen Chempark (South West in Fig. 16) stating that "CO2 sequestration in the products was accounted for based on the stoichiometric C contained in bio-naphtha used to produce the products".
Fig 16 - Ineos crackers n°4 and N°5 at the Doormagen Chempark in Germany

However qualitative the audits performed by the certification bodies, their accreditations only establish compliance and intentions to produce biomaterials, but no actually produced quantities. What's more, the underlying audit mechanisms, methodologies and results are kept hidden to the public, preventing any verification of sustainability claims.
At portfolio planning PLUS we believe in quantification and actual mass balances of industrial units. After all, "ESG should be boiled down to one simple measure: emissions" [19]. We have developed a methodology to capture all production plants capacities, consumptions and productions, to produce detailed process mass balances, also capturing the mass of emissions such as in this model of an Atmospheric Distillation Unit (ADU), where fuel consumption to power the unit and corresponding CO2 flue gas quantities are determined (Fig. 17).
Fig. 17 - Mass Balance and Emissions of an ADU
When applied to any type of chemical process, our unique methodology is able to quantify and comparatively assess carbon footprints down to the precise determination of renewable carbon content when employing renewable fuels and feedstock in energy and chemical plants. It is one of our development milestones to integrate this approach to complete value chains with the ultimate objective to determine Scope 3 emissions.
Last but not least, portfolio planning PLUS is a fully transparent, open-access platform, building on the power of the global community of experts and specialists. We invite you to join the collective effort of mapping the whole world of energy and chemicals by collating data, collaborating on modelling operations, production sites and structures. It is free and will remain so, and you can also use your Linkedin login to do so.
_________________________________________________________________________
REFERENCES
[1] nova-Paper #12 on renewable carbon. 2020-09. "Renewable Carbon – Key to a Sustainable and Future-Oriented Chemical and Plastic Industry". Renewable Carbon Initiative
[2] 2-Ethylhexanol Pro 25. perstorp.com
[3] 06 October 2020. "Perstorp introducing world's first renewable Oxo products". perstorp.com
[4] Sotelo-Boyás, Rogelio & Trejo-Zarraga, Fernando & Hernandez-Loyo, Felipe. (2012). Hydroconversion of Triglycerides into Green Liquid Fuels. http://dx.doi.org/10.5772/48710
[5] Jaakko Nousiainen, Arto RISSANEN, Andrea GUTIERREZ, Teemu LINDBERG, Heli LAUMOLA, Pekka Knuuttila. US10240095B2: "Process for producing biofuel and biofuel components"
[6] Jaakko Nousiainen, Petri Kukkonen, Jari Kotoneva, Teemu LINDBERG, Timo Äijälä. US10023810B2: "Process for producing hydrocarbons from crude tall oil and tall oil pitch"
[7] Jozef Mikulec, Andrea Kleinová, Ján Cvengroš, L'udmila Joríková, Marek Banič. "Catalytic Transformation of Tall Oil into Biocomponent of Diesel Fuel". International Journal of Chemical Engineering. vol. 2012. Article ID 215258. 9 pages. 2012. https://doi.org/10.1155/2012/215258
[8] Argus Bionaphth for ARA. argusmedia.com
[9] 18 Mar 2021. Nova Institute. "Bio-based Naphtha and Mass Balance Approach – Status & Outlook, Standards & Certification Schemes". renewable-carbon.eu
[10] Polymers for a Sustainable Environment and Green Energy, T.W. Abraham, R. Höfer, in Polymer Science: A Comprehensive Reference, 2012, 10.03.2.1.2 Other vegetable oils. Source: sciencedirect.com
[11] Marcos, João and João Marcos. “Modelling of Naphtha Cracking for Olefins Production.” (2017), semanticscholar.org
[12] Redefining Energy podcast, Episode n°62. "ESG investing: A force for good or blah blah blah?", Nov 2021
[13] The mass balance approach. International Sustainabiity & Carbon Certificaton (ISCC).
[14] UPM BioVerno naphtha for replacing fossil raw materials. upmbiofuels.com
[15] 11 Feb 2020. "INEOS and UPM Biofuels announce supply agreement for renewable raw materials to make plastic". ineos.com
[16] Frank Esposito. 12 Feb 2020. "Ineos signs long-term supply agreement for bioattributed PVC". Plastic News.
[17] Rebecca Coons. 30 Sep 2019. "Dow set to boost renewable naphtha use at Dutch cracker". biofueldigest.com
[18] 12 March 2020. Innovation in Textiles. "DSM introduces bio based Dyneema".
[19] 21 Jul 2022. Three letters that won’t save the planet. The Economist.